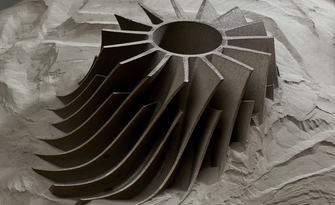
Synergizing Additive Manufacturing and Traditional Machining for Optimal Production Efficiency
In recent years, the debate on additive technologies has grown more and more, with the reflection on whether they represent an alternative to traditional chip removal technologies. The point of view that best reflects our thinking and the current state of the industry is that the two different visions, the additive and the subtractive, are not alternatives or substitutes, but complementary. The challenge is therefore to better understand how to proceed with a fruitful integration of the two modalities within a production context. This evolution in the approach reflects a nuanced understanding of the strengths and limitations inherent in both approaches, aiming to leverage their combined capabilities for enhanced production efficiency and innovation.
Traditional manufacturing, encompassing methods like CNC machining, injection molding, and sand casting, has long been the cornerstone of mass production. Its strengths lie in its ability to produce high volumes quickly and cost-effectively, ensuring a consistent output of parts with minimal deviation from the original design. This efficiency is particularly beneficial when manufacturing simple, uniform products in large quantities, where the cost-per-unit decreases due to the amortization of upfront tooling costs across a vast production scale.
However, traditional manufacturing is not without its drawbacks. The subtractive nature of these processes often leads to significant material waste, particularly in machining where chips are an unavoidable byproduct. Additionally, once a tool or mold is created, the ability to modify the design is severely limited, inhibiting flexibility and responsiveness to market changes. Moreover, for low to medium production levels, the cost-effectiveness diminishes, as the initial tooling expenses cannot be spread over a large number of units, impacting profitability.
Additive Manufacturing, or industrial 3D printing, operates on an entirely different principle, constructing products layer by layer based on a digital model. This method has gained traction in industries such as aerospace, medical, and dental due to its unparalleled customization capabilities and the ability to create complex geometries unachievable through traditional means. Material flexibility is another significant advantage, which allows the selection of various materials and alloys that are even more performing than the original ones, selecting them according to specific application needs, rather than being constrained to the range of materials that can usually be machined.
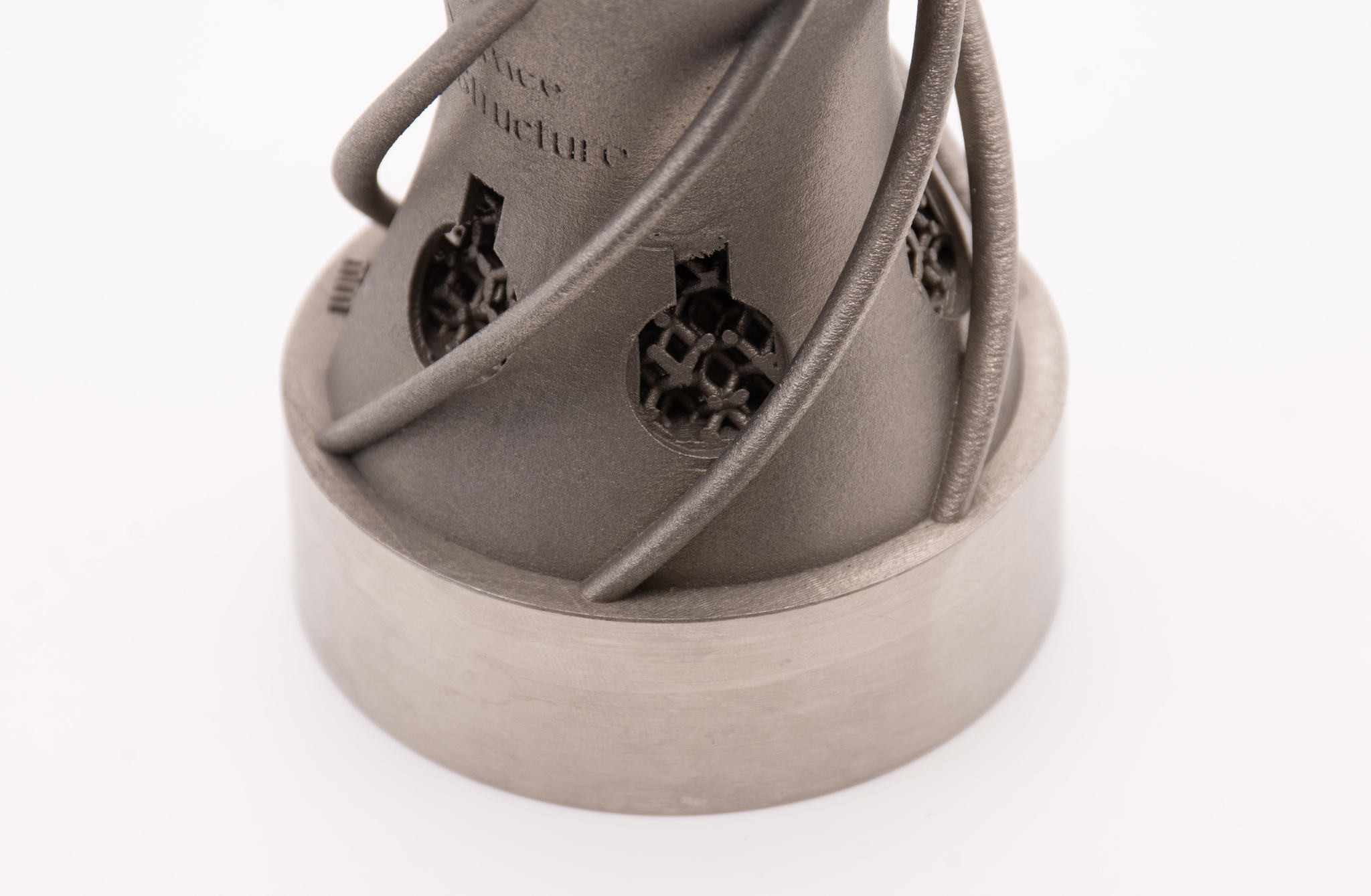
The concept of digital warehousing epitomizes the agility of Additive Manufacturing, where a library of digital designs can be rapidly prototyped or produced in small batches, circumventing the need for extensive physical inventory. Furthermore, Additive Manufacturing enables part consolidation and design alteration with ease, without the necessity for individual tools for each product variant.
Despite these advantages, metal additive manufacturing also faces challenges. The upfront cost of additive manufacturing systems can be a barrier, and depending on the needs of the finished product, post-processing may be required that adds time and complexity to the manufacturing process.
At Prima Additive, we are committed to providing solutions that make additive manufacturing an increasingly accessible and competitive technology, maximizing customer satisfaction. Through ongoing dialogues with our industry partners and analyzing numerous practical cases of metal component production, we recognize the growing interest in integrating traditional manufacturing techniques with Additive Manufacturing. This integration allows us to harness the high-volume efficiency and consistency of traditional methods while leveraging the flexibility and innovative capabilities of Additive Manufacturing. Our approach is to create synergies between these technologies, providing our clients with the best of both worlds – the efficiency of traditional manufacturing and the customization and complexity achievable with Additive Manufacturing.
Integrating Additive Manufacturing and Traditional Metalworking for Advanced Production
Additive Manufacturing and traditional metalworking techniques, often seen as distinct or even competing methods, are thus increasingly being recognized for their potential in collaborative and hybrid applications. This convergence of methodologies opens a realm where the respective strengths of each can be harnessed in unison, leading to an optimized manufacturing process for metal parts.
At the heart of this integration is the understanding that each approach offers unique advantages. Traditional metalworking techniques, including CNC machining and chip-removal processes, excel in producing high volumes efficiently and consistently. They are especially suited for parts with simpler geometries or when a high degree of surface finish and tolerance accuracy is required. In contrast, Additive Manufacturing shines in its ability to create complex, intricate geometries that would be challenging, if not impossible, to achieve with traditional methods. Its layer-by-layer construction allows for greater design freedom, customization, and the ability to rapidly prototype.
By combining the two different types of technologies, it is therefore possible to produce components with complex geometries while maintaining the high precision and finish quality characteristic of CNC machining.
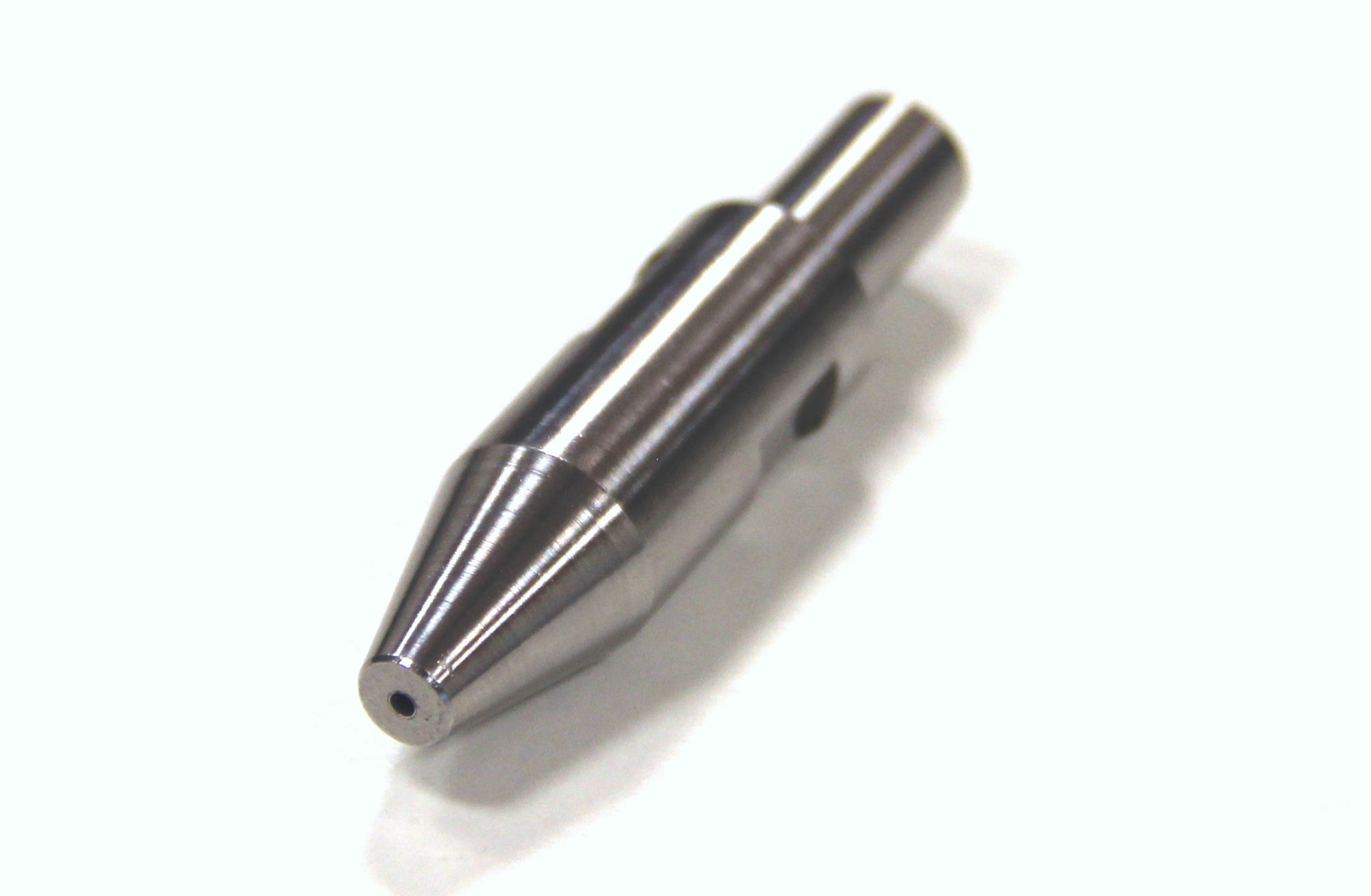
This growing interest in this kind of integration is increasingly embraced across various sectors of the manufacturing industry. The rationale behind this trend is clear - by combining the strengths of both approaches, manufacturers can achieve a level of efficiency, versatility, and innovation that is greater than the sum of its parts.
For instance, a part can be rapidly prototyped using Additive Manufacturing, allowing for easy testing and modification, followed by high-volume production using traditional machining. Alternatively, complex components can be initially shaped using Additive Manufacturing and then finished with machining to achieve the desired surface quality and dimensional accuracy. This hybrid approach can lead to significant cost savings, especially in scenarios where complex geometries are essential but require the high finish quality of traditional machining.
At Prima Additive, we are keenly aware of the immense potential that lies in the integration of these two manufacturing realms. Our continuous engagement with industry partners and analysis of practical production scenarios reveals a strong interest in leveraging both Additive Manufacturing and traditional techniques for metal component production. On the other hand, this approach aligns perfectly with our commitment to innovation and customer satisfaction, as it offers a more comprehensive range of solutions to meet the diverse needs of our clients.
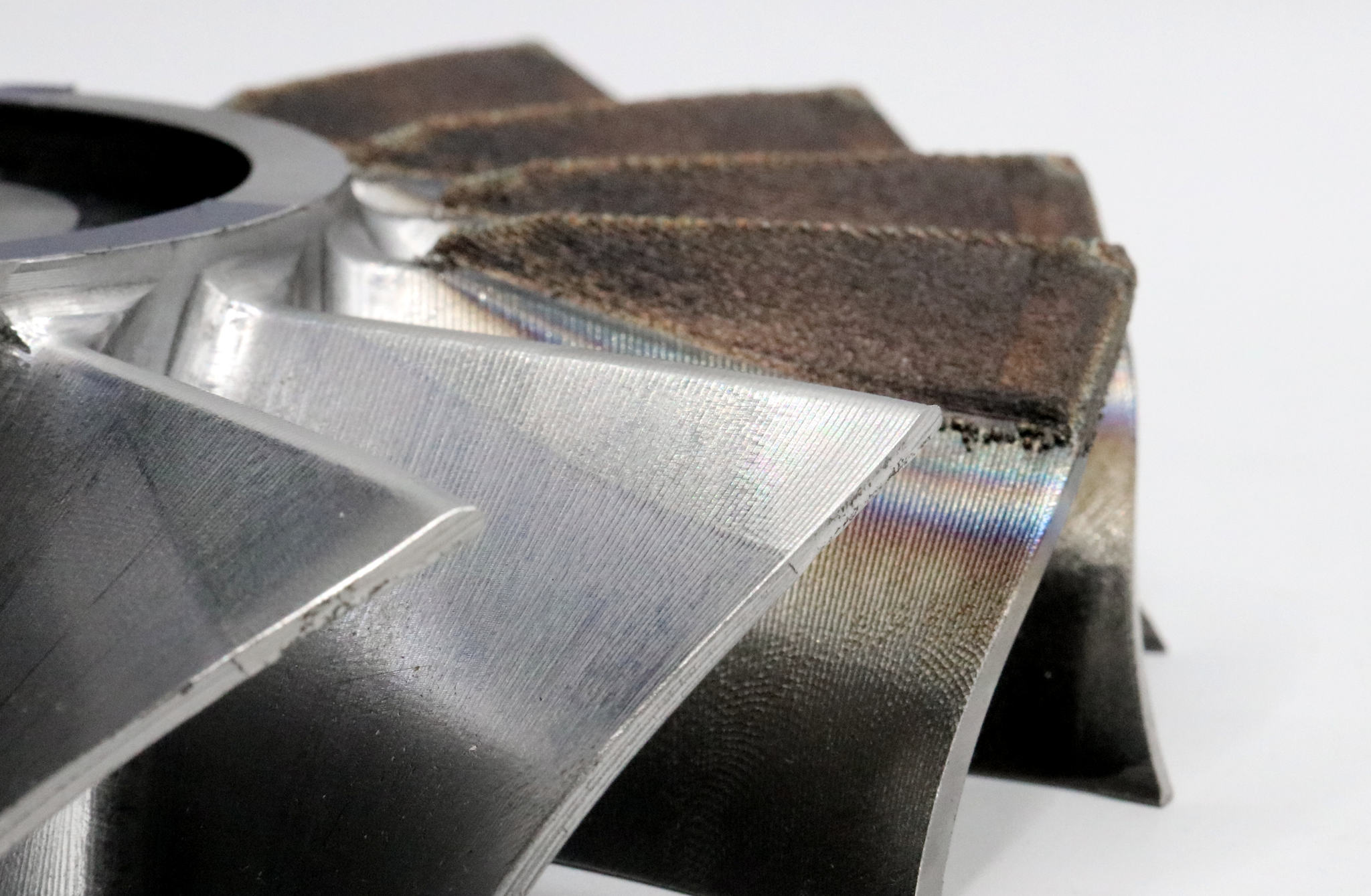
Harnessing the Power of Combined Technologies in Diverse Industries
Prima Additive's client base spans across various industrial sectors, including aerospace, automotive, medical, energy, and tooling. The integration of Additive Manufacturing with traditional chip-removal processes presents a substantial resource for these industries, each with its unique challenges and demands.
In aerospace and automotive, where precision and strength are paramount, the integration can lead to the production of lightweight yet robust components. The medical sector can benefit from the combined technologies in creating intricate, patient-specific implants. For energy and tooling industries, this integration can result in highly durable and efficient components.
Prima Additive specializes in two Additive Manufacturing processes: Powder Bed Fusion and Direct Energy Deposition. While the first is particularly adept at creating complex, finely detailed parts and can be complemented by traditional machining for achieving high-precision surfaces or specific tolerances, the latter is ideal for repairing or adding material to existing components and can be integrated with traditional methods to enhance the functionality or lifespan of parts. In effect, both these Additive Manufacturing processes offer unique advantages when integrated with traditional chip-removal techniques.
Prima Additive is at the forefront of exploring these integrated solutions. We invite companies from all sectors of the production industry to collaborate with us in exploring how the integration of Additive Manufacturing and traditional machining can elevate their production capabilities. Whether it's through enhancing product performance, reducing production costs, or driving innovation, our team is ready to evaluate and implement integrated solutions tailored to your specific needs. Contact Prima Additive today to discover how our expertise in combined manufacturing technologies can benefit your business.
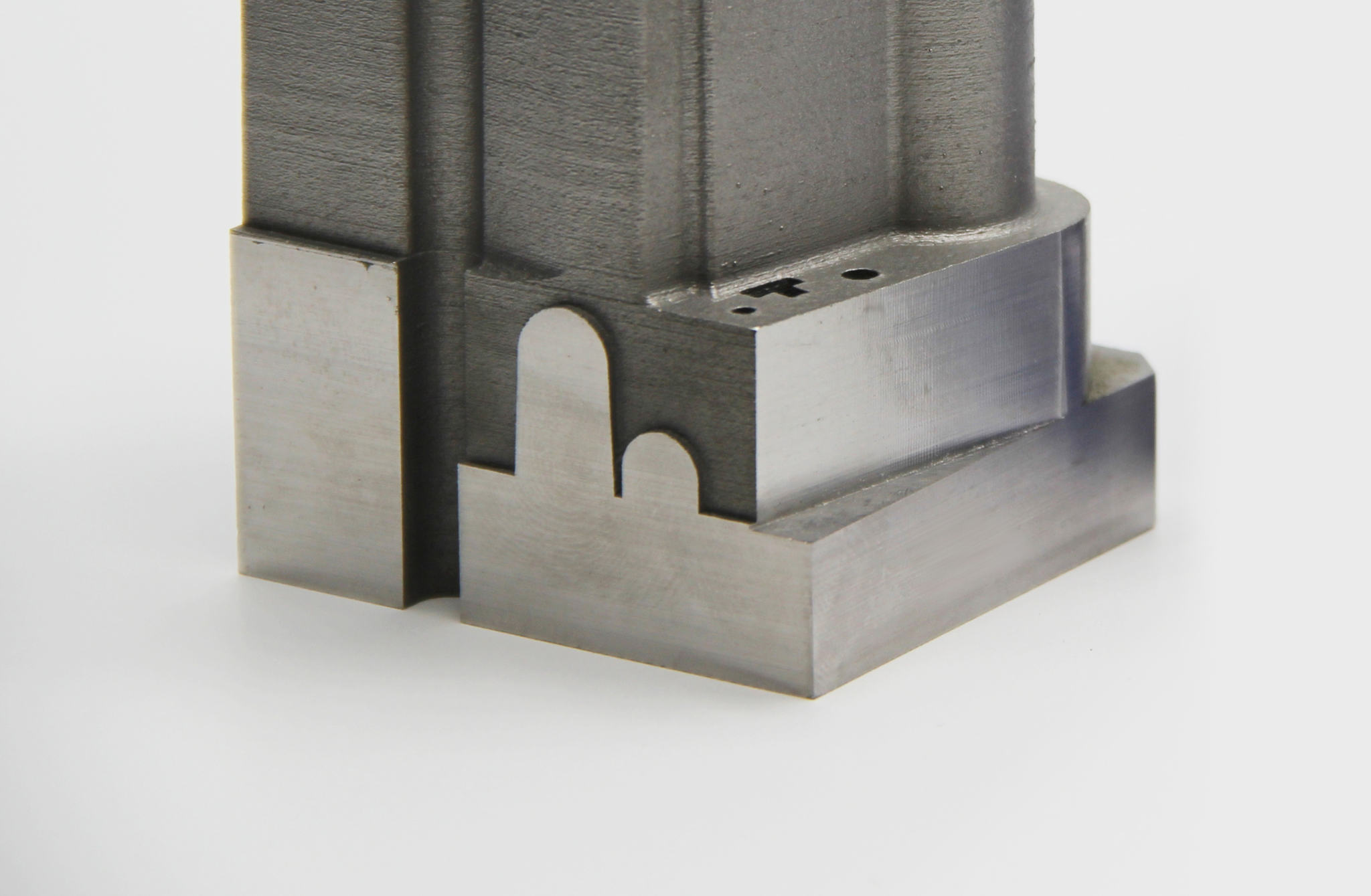