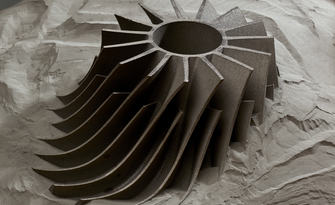
Remote care
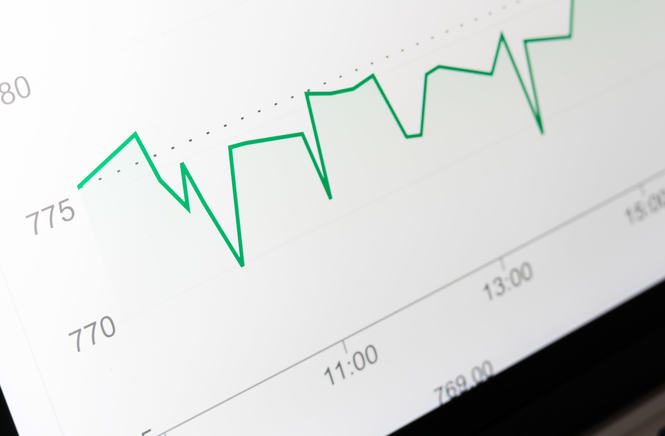
The era of Industry 4.0 has revolutionized the way we manage technical support. In the past, problem resolution followed a rigid and costly process: the machine stopped, a technician was sent on-site to diagnose the issue, and only then was the repair carried out. Today, with Prima Additive’s Remote Care service, maintenance becomes proactive and predictive, reducing downtime and optimizing the performance of additive manufacturing systems.
Remote Care allows for real-time machine monitoring, detecting anomalies and enabling rapid intervention to prevent unexpected failures. Through continuous performance analysis, our system helps anticipate malfunctions, optimizing the machine's lifecycle and ensuring maximum productivity.
When an issue arises, our technical team can perform remote diagnostics, providing fast solutions without the need for an on-site visit. If an in-person intervention is necessary, the issue is already identified in advance, shortening repair times and ensuring a faster production restart.
To ensure fast and effective assistance, Prima Additive integrates advanced remote support technologies, including:
Using smartphones or tablets, field technicians can connect with our experts and share real-time images and videos. Our specialists can observe the issue directly on the machine, perform precise diagnostics, and provide detailed instructions for resolution—reducing the need for travel and ensuring instant support.
With the use of mixed reality smart glasses, technicians can interact with holograms and 3D models directly in the workspace. This technology allows them to:
✅ Enhanced operational efficiency: less downtime, higher productivity.
✅ Fast problem resolution: immediate diagnostics and support.
✅ Lower service costs: fewer on-site visits and reduced travel expenses.
✅ Continuous support and advanced training: access to detailed information for optimal machine management.
With Remote Care, maintenance becomes proactive and intelligent, keeping your equipment running at peak performance
Application support
Open innovation
Circular economy inspired
© Prima Additive S.r.l. | Corso Re Umberto, 54 - 10128 Torino (TO) Italia | Share Capital € 116.860,77 fully paid up | VAT 11434740012 - C.C.I.A.A.Torino 1213183 | Reg. Impr. Torino n. 11434740012