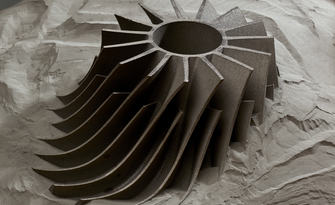
FAQ
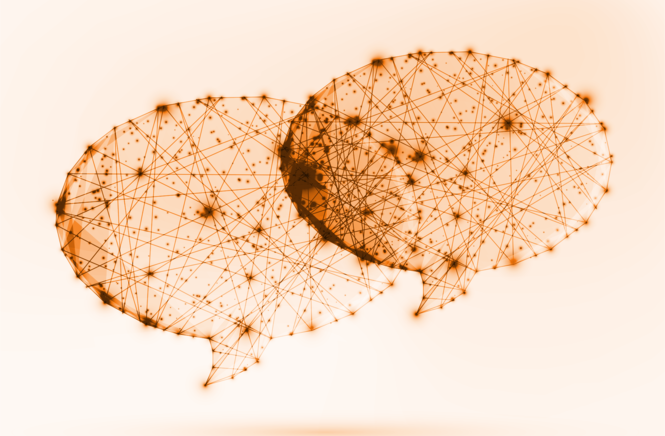
Frequently asked questions
Additive Manufacturing has no more secrets.
Which metals can I use on a Prima Additive machine?
Prima Additive offers a comprehensive selection of metal powders, ranging from aluminium to nickel, steel, titanium, as well as copper alloys. We develop the right process parameters to set up your machine and ensure quality and repeatability. We are always willing to research and develop new materials suitable for additive manufacturing to satisfy every need.
What is the minimum size I can produce?
The minimum size that can be achieved is a line measuring 0.12-0.15mm in width with our Powder Bed Fusion machines. This level of detail allows you to create complex shapes even on tiny components.
What is the maximum size?
The maximum size depends on the volume of the machine: Prima Additive solutions range from a volume of Ø 150mm; h=160mm in our 150 series with Powder Bed Fusion technology, up to a working area of 2032 x 1016 x 1829 mm in our Direct Energy Deposition LASERDYNE 795 machine.
Can I combine different materials on the same object?
With our Direct Energy Deposition machines, you can work with up to two different materials at the same time, thanks to a powder feeder equipped with two separate metal powder hoppers. You can also coat or add parts to a metal component using a different material to the original one.
What is the average time needed to produce an object?
It is not possible to establish an average time to produce an object. Production speed depends on the application and is not exclusively linked to the part's volume. It is influenced by several factors, such as the diameter of the laser focal point, the thickness of the powder layer, the material, the machine's working area or the number of lasers.
What level of detail can be achieved with Prima Additive machines?
For Powder Bed Fusion technology the accuracy of our machines ranges from +/- 0.05mm for small parts to +/- 0.1mm for large parts, while for Direct Energy Deposition technology our solutions have an accuracy of +/- 0.2mm.
I own a 3D laser machine. Can I convert it into an additive manufacturing system?
Yes, you can turn your 3D laser machine into a metal additive manufacturing machine with our new Direct Energy Deposition Kit. The kit includes all the equipment required for direct energy deposition applications: an innovative and multifunctional laser head, a highly efficient laser source, and a highly reliable powder feeder.
I currently produce mechanical components with traditional CNC machines. How do I know if I can make the same products using additive manufacturing and if it is suitable for my business?
To answer this question, we have created this page Request an application assessment.
On this page, you can send us a 3D model of the part you want to create: our experts will assess your business case and send you a complete application assessment. Free of charge.
I don't know much about additive manufacturing. How can I get the skills I need to make the most of this technology?
Our team of specialized engineers is always at your side to guide you towards adopting this technology. We offer training programs and upgrades to enable you to make the most of our machines and their software, maximizing production and quality. We provide training and support from the investment appraisal phase to after-sales service.
Can Prima Additive systems be integrated into automated production lines?
Yes. One of Prima Additive’s key strengths lies in designing modular and scalable systems that can be integrated into fully automated production lines. Our solutions are compatible with industrial automation standards and are developed in collaboration with partners like COMAU for the highest level of integration and productivity.
How does Prima Additive support certification and qualification of parts?
We offer a complete support path: from process parameter definition and material testing to application-specific validation. For sectors such as aerospace, energy, or medical, we help you develop a comprehensive qualification strategy and provide the data necessary to meet international standards.
Do Prima Additive machines use open or closed parameters?
Prima Additive systems are based on an open parameter philosophy, which gives users the freedom to develop or optimize parameters according to their specific applications. This allows for maximum flexibility, particularly in R&D or for advanced users.
Is it possible to process reflective or special materials, like copper or precious metals?
Yes. Prima Additive offers specialized laser sources, including green and blue lasers, that allow the processing of highly reflective materials such as copper, gold, and other precious metals. These options are ideal for applications in electronics, jewelry, and energy.
Take advantage of our services
Application support
Transforming ideas into industrial reality
Metal Additive Manufacturing offers limitless opportunities for innovation, but successfully integrating it into an industrial workflow requires the right expertise and support.
Design support
Redefining design for performance and efficiency
The true power of metal additive manufacturing (AM) lies in its ability to create complex geometries that were once impossible with traditional methods.
Qualification and certification
Ensuring quality and compliance in additive manufacturing
In metal additive manufacturing, the quality of a component is not only measured in terms of dimensional accuracy and mechanical properties but also in its ability to meet strict industry certification standards.