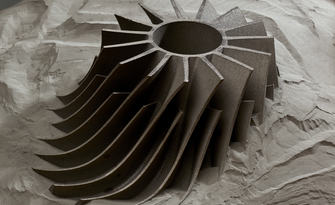
Global assistance and service
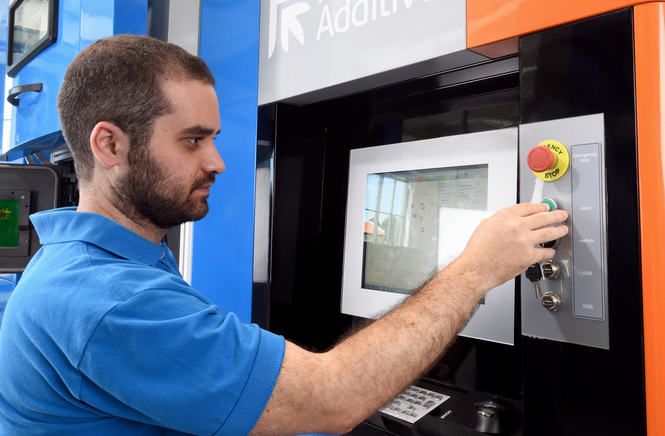
Reliable Additive Manufacturing support: anytime, anywhere
Ensuring the continuous operation and optimal performance of your additive manufacturing system is our priority.
Ensuring the continuous operation and optimal performance of your additive manufacturing system is our priority.
With Prima Additive’s global assistance network, you receive fast, high-quality support wherever your business operates. Our international team of specialized technicians is available to assist with remote diagnostics, on-site interventions, and preventive maintenance programs designed to keep your production running efficiently.
Through our global network of certified partners and technical collaborators, we provide:
✅ Remote assistance and diagnostics – Our experts can remotely connect to your machine, conduct a detailed analysis, and resolve most issues without on-site intervention.
✅ On-site support – Our local service centers provide fast response times with skilled technicians ready to assist whenever needed.
✅ Spare parts availability – We ensure quick delivery of original spare parts, reducing unplanned downtime and ensuring maximum system availability.
✅ Certified training programs – Our training sessions equip operators and engineers with the necessary skills to optimize machine performance and efficiency.
With comprehensive support services, we ensure your additive manufacturing systems remain operational, productive, and cost-effective.
Our service philosophy focuses on carefully planned maintenance to prevent breakdowns and optimize machine longevity. Scheduled maintenance helps detect potential issues early, avoiding costly downtime and ensuring continuous production.
✔ Replacement of key components & spare parts
✔ Comprehensive machine condition assessment
✔ Performance adjustments & fine-tuning
✔ Functional system checks
✔ Recommendations for corrective actions
✔ Reduced unexpected failures
✔ Planned, short maintenance downtimes
✔ Improved Overall Equipment Effectiveness (OEE): availability, speed & quality
✔ Lower corrective maintenance costs
✔ Enhanced long-term reliability of your AM system
For any unexpected issues, our high-quality corrective maintenance ensures rapid recovery, minimizing disruptions to your workflow.
When production layouts change, or machines need to be transferred between facilities—even internationally—our machine relocation service ensures a smooth transition.
We provide:
✔ Relocation planning and site preparation
✔ Project management for seamless execution
✔ Professional disassembly, transportation and reinstallation
✔ Machine calibration, testing and safety compliance
Whether you are upgrading your production facility or moving your machine to a new site, our relocation service guarantees minimal downtime and maximum efficiency.
With Prima Additive’s worldwide service & assistance, you gain:
Ensure maximum uptime and peak performance of your additive manufacturing systems with our dedicated global support.
Application support
Open innovation
Circular economy inspired
© Prima Additive S.r.l. | Corso Re Umberto, 54 - 10128 Torino (TO) Italia | Share Capital € 116.860,77 fully paid up | VAT 11434740012 - C.C.I.A.A.Torino 1213183 | Reg. Impr. Torino n. 11434740012