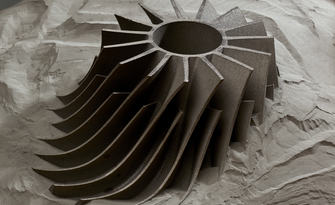
Nickel alloys for DED
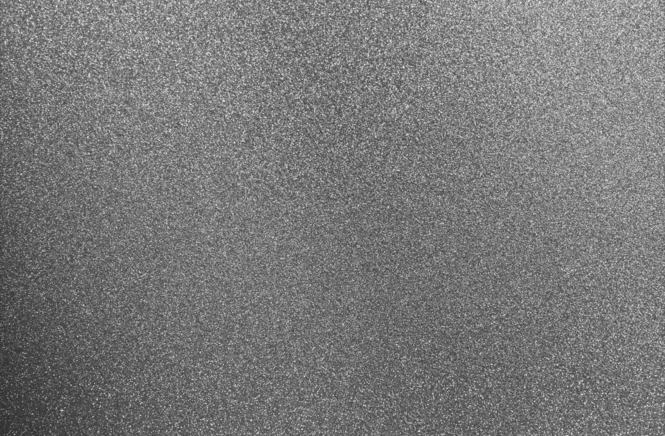
Materials for Direct Energy Deposition
For stress and corrosion resistant parts.
As the field of metal additive manufacturing evolves, the exceptional qualities of nickel alloys and nickel powders emerge as pivotal. Prima Additive harnesses the power of innovative Direct Energy Deposition (DED) technology, propelling these materials to the forefront of industrial solutions. This approach offers industries unparalleled capabilities to withstand extreme conditions, showcasing the remarkable potential of nickel in additive manufacturing.
Why Nickel Alloys? A Blend of Strength and Versatility
Nickel superalloys, recognized for their unparalleled stress and corrosion resistance, are ideally suited for high-performance industrial applications operating within the demanding temperature ranges of 500 °C to 1000 °C. Prima Additive's state-of-the-art DED machines are engineered to harness the full potential of these alloys, including the renowned Inconel and Hastelloy nickel alloys, bringing your most ambitious projects to life with unmatched precision and durability.
The Advantages of Direct Energy Deposition with Nickel Alloys
High Yield
Maximize material utilization and efficiency, reducing waste and optimizing production processes
Exceptional Wear and Friction Resistance
Extend the lifespan of components even in the most demanding operational conditions
Outstanding Antioxidant and Anticorrosive Properties
Ensure peak performance in aggressive environments, safeguarding your investments against degradation
High-Temperature Corrosion Resistance
Maintain integrity and functionality at elevated temperatures, a critical attribute for aerospace, automotive, and energy sectors
Featured Nickel Alloys Compatible with Prima Additive's Machines
- Inconel 625 & 718: Offering a blend of high strength, durability, and resistance to environmental effects, these alloys are perfect for aerospace, marine, and energy applications.
- Hastelloy X: Renowned for its exceptional strength and oxidation resistance at high temperatures, making it ideal for furnace and chemical processing applications.
Beyond the standard
The mentioned materials represent just a glimpse of what's possible with Prima Additive's versatile machines. Our technology is designed to work with any type of material made by any manufacturer, thanks to open parameters that allow for limitless creativity and innovation. Whether you're exploring the potential of nickel alloys or other advanced materials, Prima Additive provides the tools and support to turn visionary ideas into tangible realities, embodying the spirit of change, competitiveness, and innovation that drives us forward.
Areas of application
Did you know that nickel alloys are widely used in these sectors?
Need to make parts using a different material?
We are at your service to research and produce new materials suitable for additive manufacturing to meet your specific needs.
We will evaluate your business case and together develop the best material for your application.
Take advantage of our services
Request an application assessment
Feasibility assessment
Let's break down the barriers to entry for Additive Manufacturing!
Application support
Transforming ideas into industrial reality
Metal Additive Manufacturing offers limitless opportunities for innovation, but successfully integrating it into an industrial workflow requires the right expertise and support.
Design support
Redefining design for performance and efficiency
The true power of metal additive manufacturing (AM) lies in its ability to create complex geometries that were once impossible with traditional methods.
Training in additive manufacturing processes
Comprehensive training for Metal Additive Manufacturing
Investing in metal additive manufacturing means embracing an innovative, high-performance technology that requires in-depth knowledge and hands-on experience to maximize its potential.
Qualification and certification
Ensuring quality and compliance in additive manufacturing
In metal additive manufacturing, the quality of a component is not only measured in terms of dimensional accuracy and mechanical properties but also in its ability to meet strict industry certification standards.
Here are our solutions for processing Nickel alloys for DED
LASERDYNE® 811
Direct Energy Deposition technology
The fastest solution for 3D manufacturing, repairs and coating with quality and precision.
Laser Next 2141
Direct Energy Deposition technology
A large machine, available in various configurations, for repairing, coating, adding custom parts.
DED kit
Direct Energy Deposition Technology