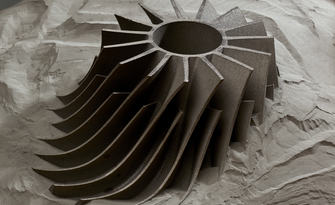
Unlocking the full potential of Titanium and Aluminum alloys with advanced DED technology
Direct Energy Deposition (DED) is one of the most versatile and scalable metal additive manufacturing technologies available today. Particularly suitable for large-scale components, complex repairs , and functional material builds, DED is gaining traction across high-value industries such as aerospace, automotive, energy, and medical. As the global manufacturing industry accelerates toward digitalization and sustainability, the use of reactive metals such as titanium and aluminum in additive manufacturing has become not only desirable, but strategic. But when it comes to processing reactive metals, DED presents unique challenges that require highly engineered safety solutions and process controls.
At Prima Additive, we have developed dedicated DED systems equipped to handle reactive materials with precision and safety in mind. Whether you're working with aluminum alloys, titanium alloys, or other reactive powders, our machines are designed to minimize risk, enhance process control, and optimize performance, thanks to two powerful technologies: inert chamber integration and localized inert gas shielding.
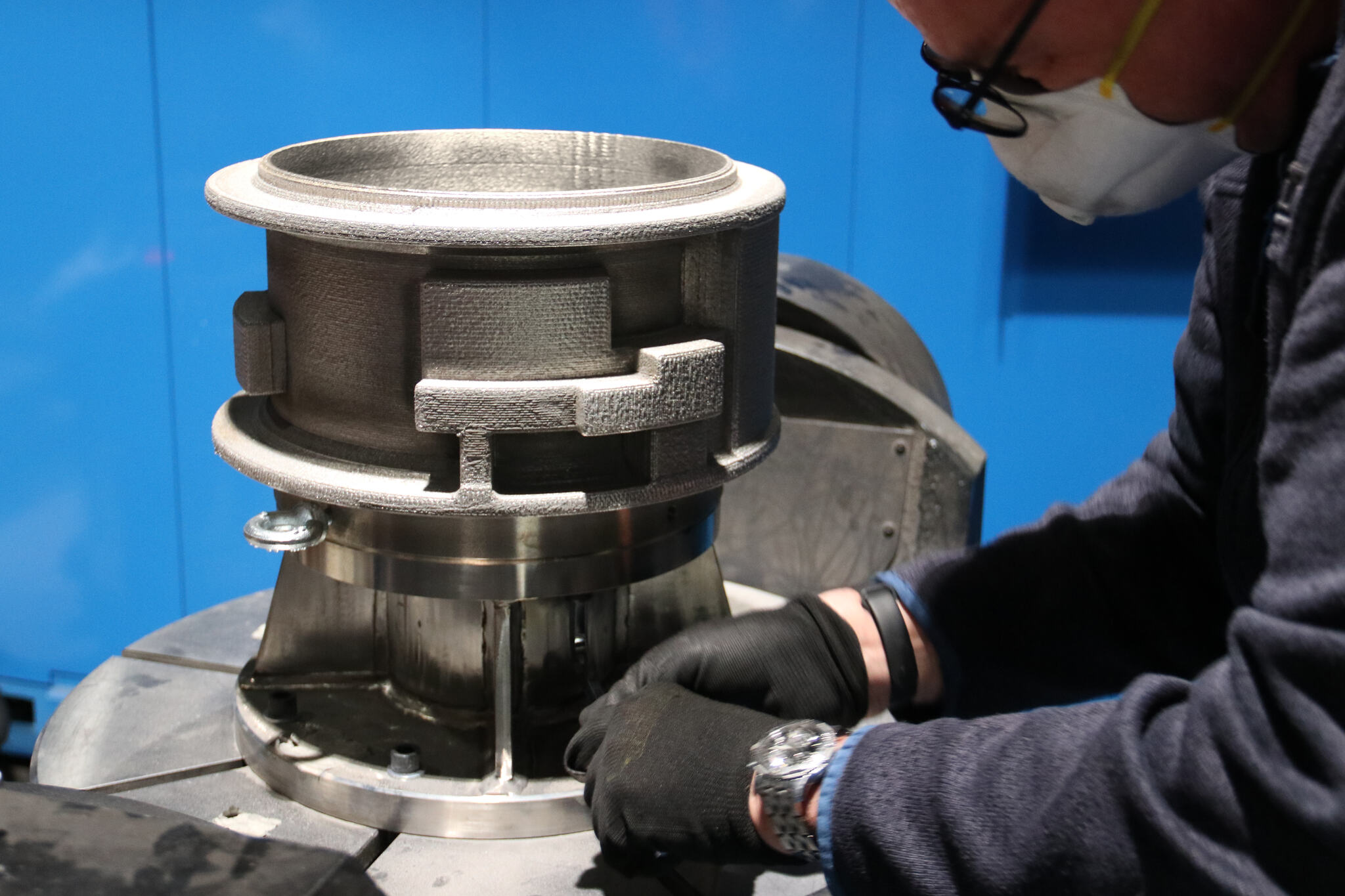
Why reactive materials need a smarter approach
DED works by melting and depositing metal, in powder or wire form, directly onto a surface using a high-powered laser. This technique allows for large build volumes, repair and hybrid applications, and the ability to manufacture geometries that are not feasible with subtractive technologies.
However, when DED is applied to reactive powders such as titanium or aluminum, the process becomes more delicate. These materials are highly sensitive to oxygen, nitrogen, and moisture, elements commonly found in ambient air. When exposed to high temperatures during the additive process, titanium and aluminum powders can oxidize rapidly or even ignite, leading to safety risks and compromised material integrity.
Without proper controls, the finished part may suffer from porosity, cracking, or inconsistent mechanical properties. Worse still, inadequate safety precautions could result in combustion events, especially during powder handling or laser exposure. These risks necessitate a more sophisticated approach to shielding the material from the atmosphere during the build process.
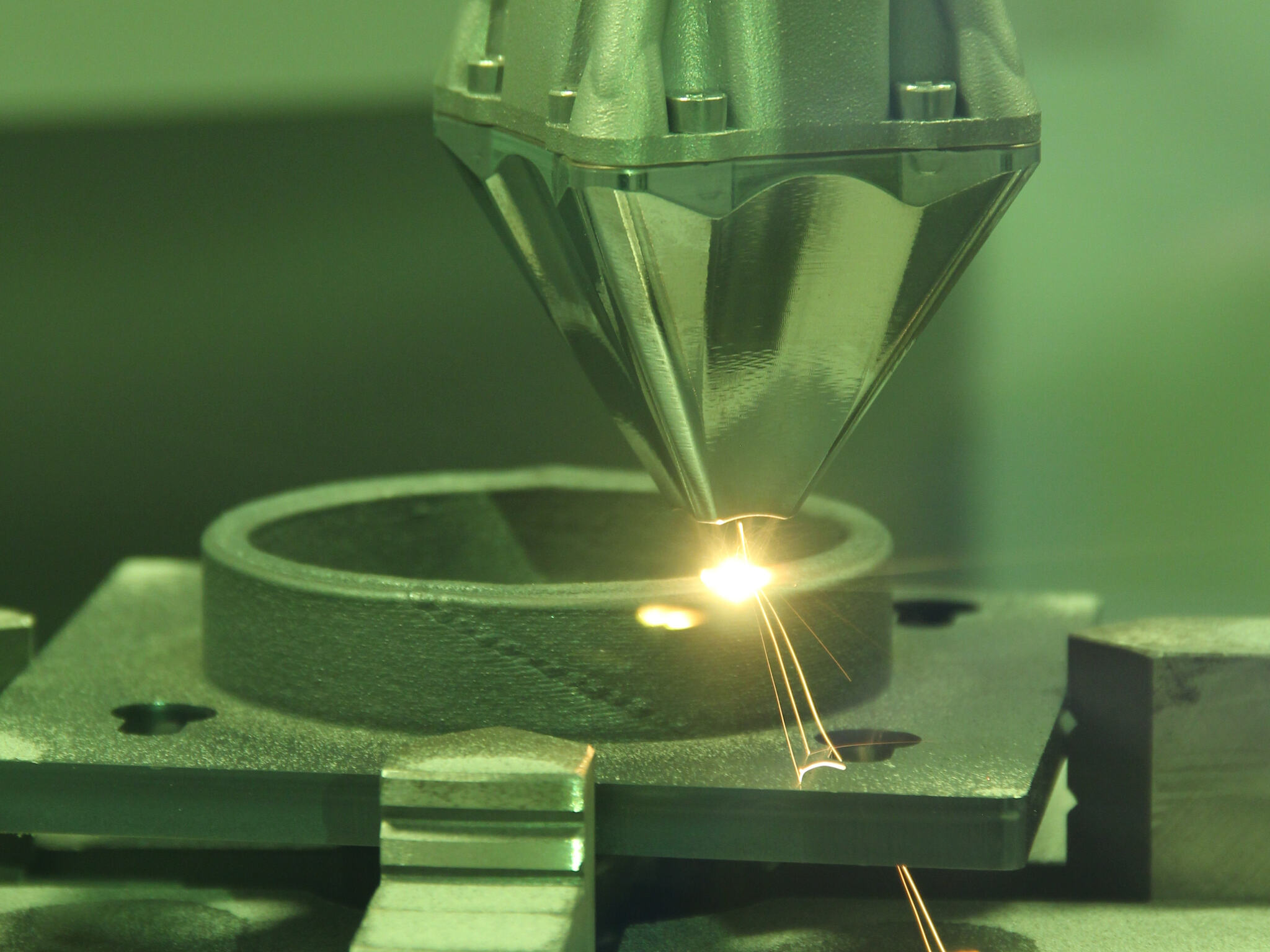
Prima Additive’s dual-safety strategy: inert chamber + inert gas shielding
To meet these challenges, Prima Additive has engineered a dual strategy that enables manufacturers to process reactive metals with complete confidence: a combination of fully inert chambers and dedicated inert gas shielding nozzles.
- Inert chamber configuration: For customers producing large or thin-walled titanium components, our systems can be built with sealed enclosures filled with argon or nitrogen. This approach ensures that the entire working area is protected from environmental contamination. It's ideal for applications where full inertization is essential to maintain material purity and performance, such as in aerospace
- Localized inert gas shielding: In scenarios where flexibility and gas savings are priorities, such as in high-mix, low-volume production or R&D environments , we offer our proprietary Inert Gas Shielding Nozzle. This component is mounted directly on the laser head and creates a focused, localized flow of inert gas around the melt pool, ensuring protection exactly where it’s needed. It drastically reduces gas consumption while still safeguarding the process
This combination gives manufacturers a tailored approach to safety and efficiency. Whether they need chamber-scale protection or targeted shielding, Prima Additive’s DED systems can be configured to match the specific requirements of the material and application.
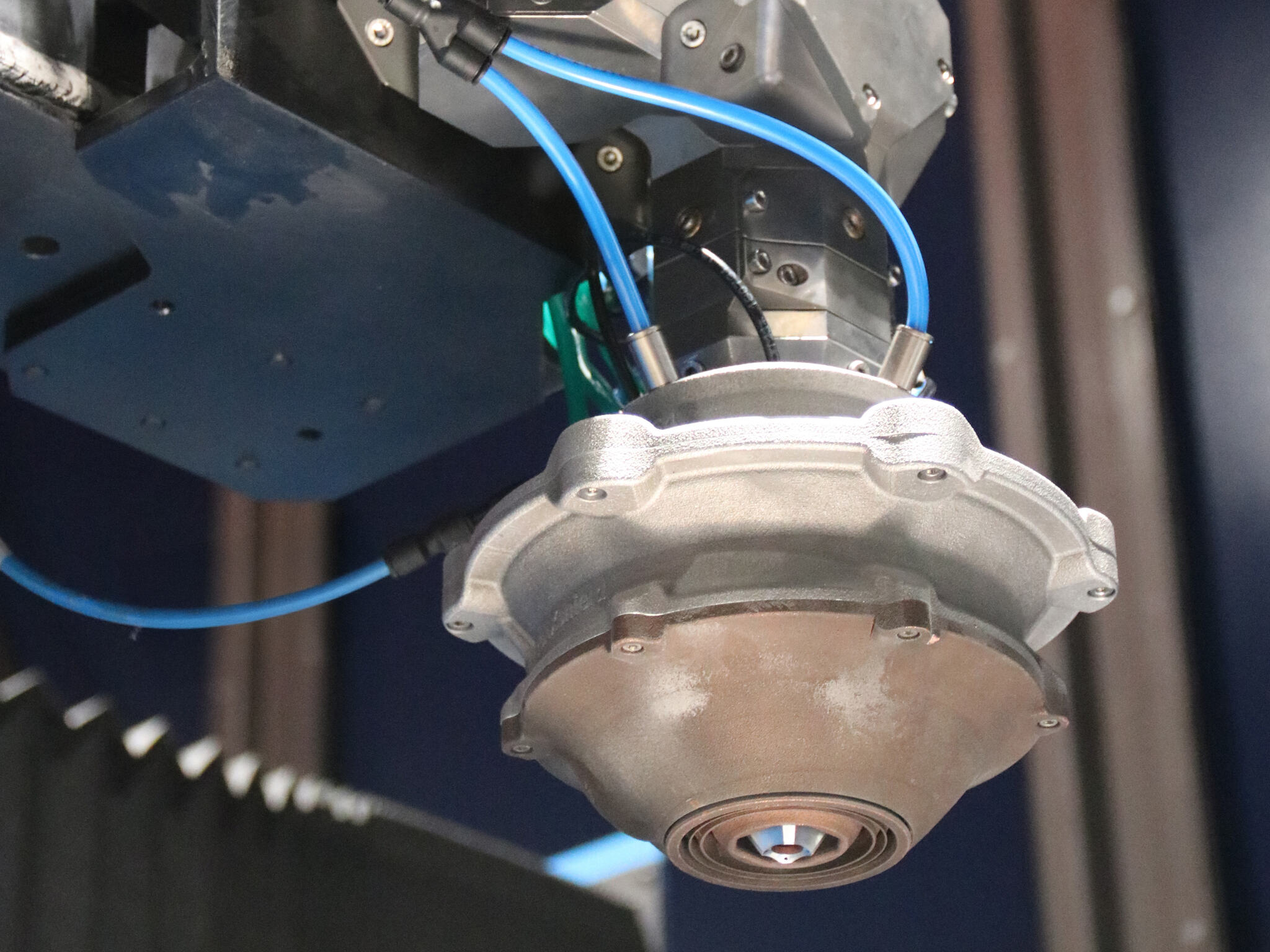
Processing Titanium and Aluminum with confidence
Titanium alloys , particularly Ti-6Al-4V, are already widely adopted in industries that require strong, lightweight, and corrosion-resistant materials. Meanwhile, aluminum alloys, including AlSi10Mg and others, are gaining attention in the additive space for their thermal conductivity and energy efficiency, especially in electric vehicles, power electronics, aerospace components, and heat exchanger applications.
Processing these alloys with DED, however, requires more than just standard parameters. From laser power modulation to scan strategies and gas flow design, every element of the process must be optimized to avoid oxidation and ensure mechanical integrity.
Prima Additive addresses this challenge not only through its hardware design but also through its open parameter philosophy. Our systems are built to accept materials from any powder supplier and to be fully customizable at the software level. This flexibility empowers our customers to experiment with new alloys, fine-tune processing parameters, and scale up quickly once the process is validated.
Our application support team plays a crucial role in this phase, guiding users through business case analysis, design optimization, parameter development, and prototype validation. This ensures that customers don’t just receive a machine: they receive a complete, scalable production solution tailored to their goals.
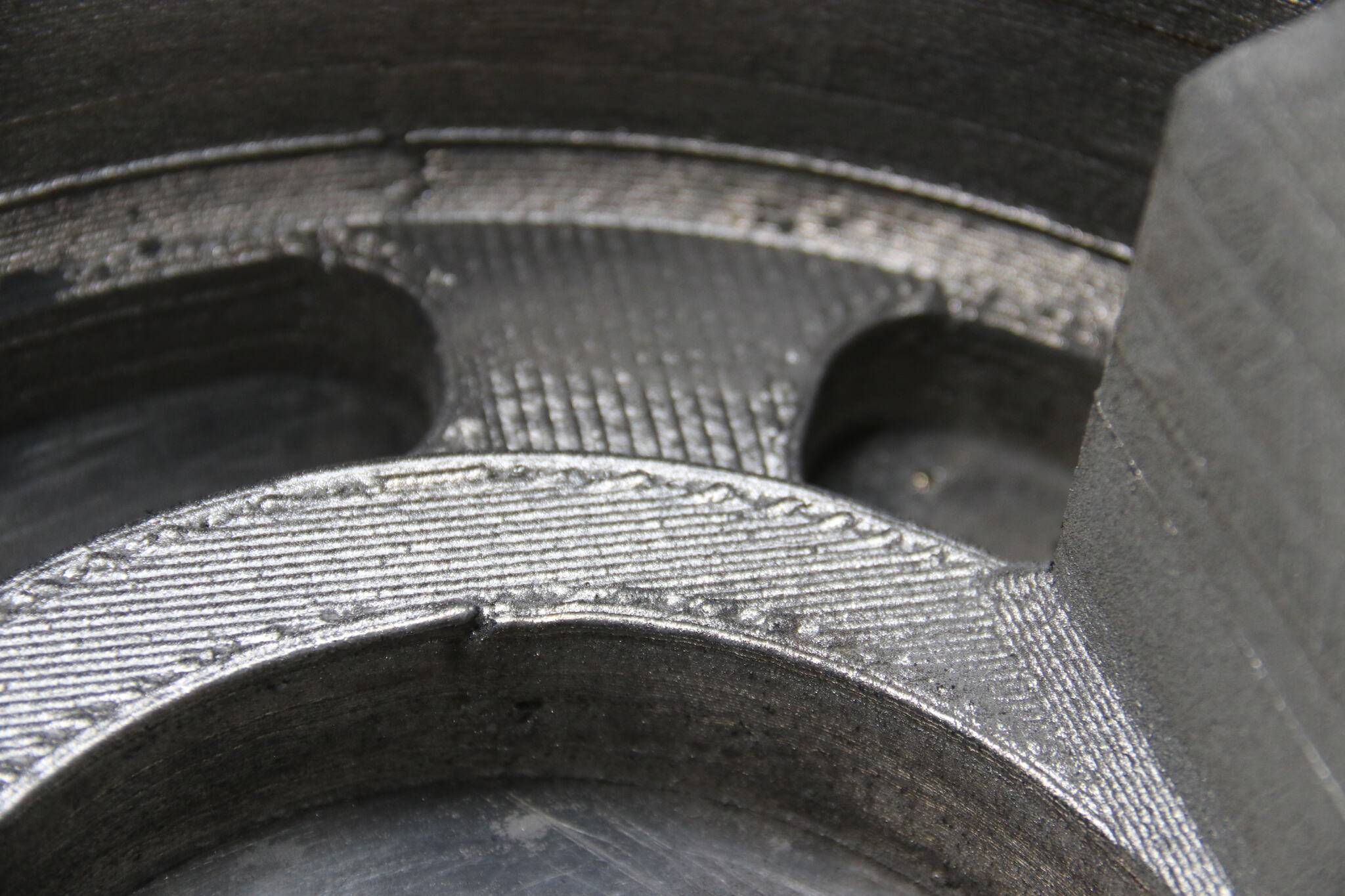
Unlocking new applications in Aerospace, Automotive, and beyond
The ability to safely process reactive metals with DED technology is a game-changer for high-tech industries. Aerospace companies can manufacture or repair lightweight titanium structural components. Automotive innovators can build complex aluminum parts optimized for electric vehicles.
What once seemed like a niche, experimental application is now a scalable, production-ready technology. With Prima Additive’s DED systems, it’s possible to go beyond prototyping and into full-scale, industrial-grade production—while maintaining control, safety, and cost-efficiency at every step.
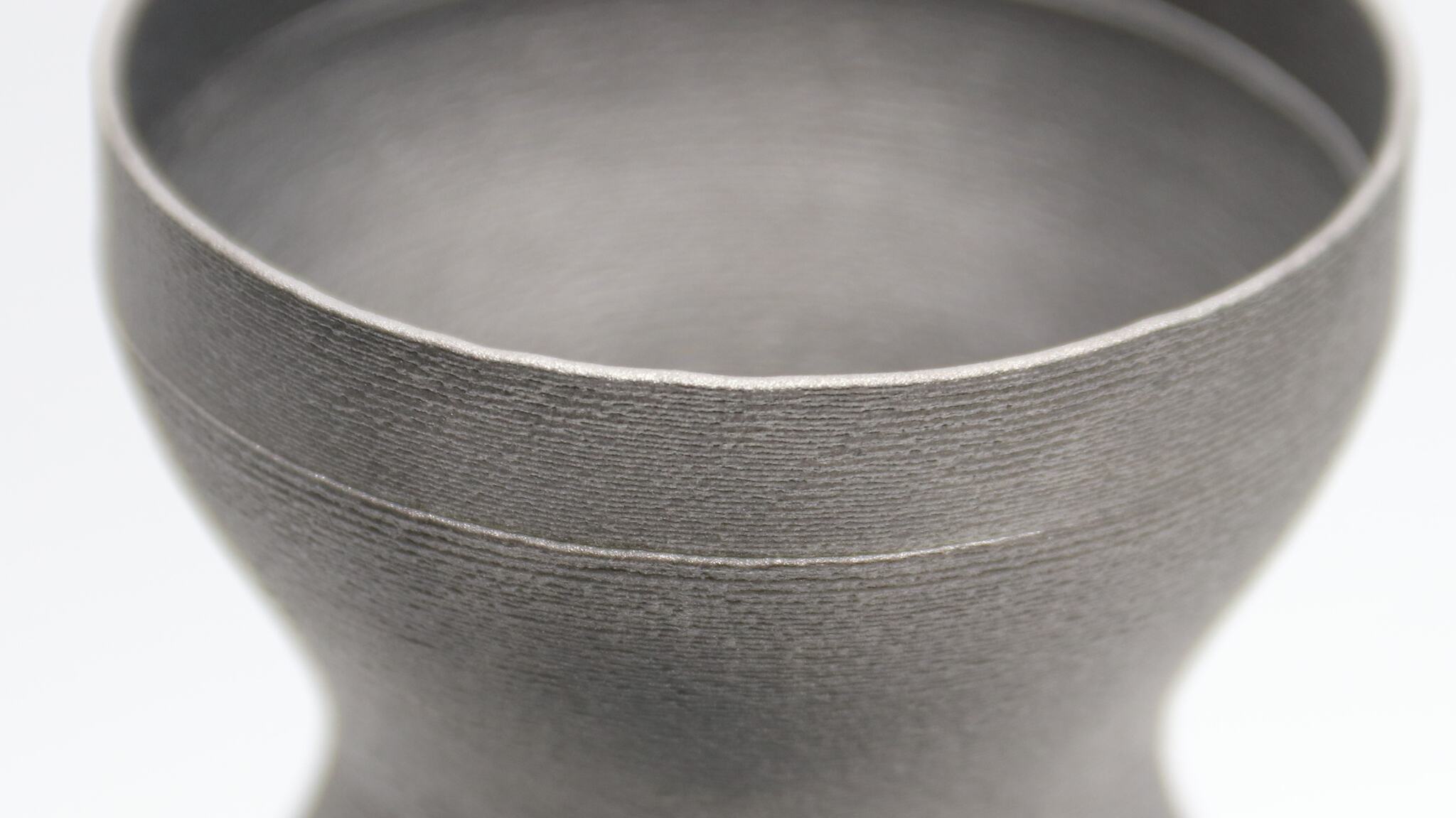
Partnering for the future of Additive Manufacturing
At Prima Additive, we are proud to lead the way in safe and efficient Direct Energy Deposition for reactive materials. Whether you're exploring additive manufacturing for the first time or scaling up to meet growing production demands, our team is ready to support you with customized solutions, deep expertise, and dedicated service.