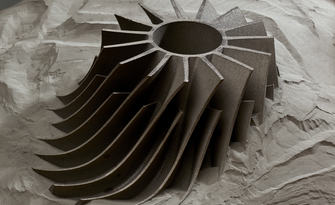
Formnext 2023: Prima Additive presents unique and configurable technologies with different wavelengths
Prima Additive will present its highly innovative and smart solutions at the Formnext trade show in Frankfurt am Main from 07 to 10 November (Hall 12.0, Stand E81).
Do you want to come and visit us at Formnext? Request a free ticket:
The first of the two machines on display, equipped with Powder Bed Fusion technology, is the Print Genius 150 Double Wavelength. This is a unique configuration on the market, featuring two lasers of different wavelengths within the same system: a 500 W infrared laser and a 200 W green laser which can work alternately on the same ⌀150 x 160 mm cylindrical work area. This solution is unique in its ability to alternate between the two lasers on the same work area, thus ensuring high performance, reliability, and accurate results.
The interchangeability of technology ensures that both conventional materials such as steel, aluminum, nickel, titanium, and cobalt chrome alloys can be processed on the same system, thanks to the infrared laser, and highly reflective materials such as pure copper or precious materials, with the implementation of the green laser. The green laser solves, indeed, the main problems of absorption, process stability, and poor efficiency that generally occur when these alloys are processed with an infrared laser. In particular, thanks to its special configuration of a 30μm spot size beam, the Print Genius 150 DW can process precious metals such as gold, with high accuracy, achieving excellent levels of quality.
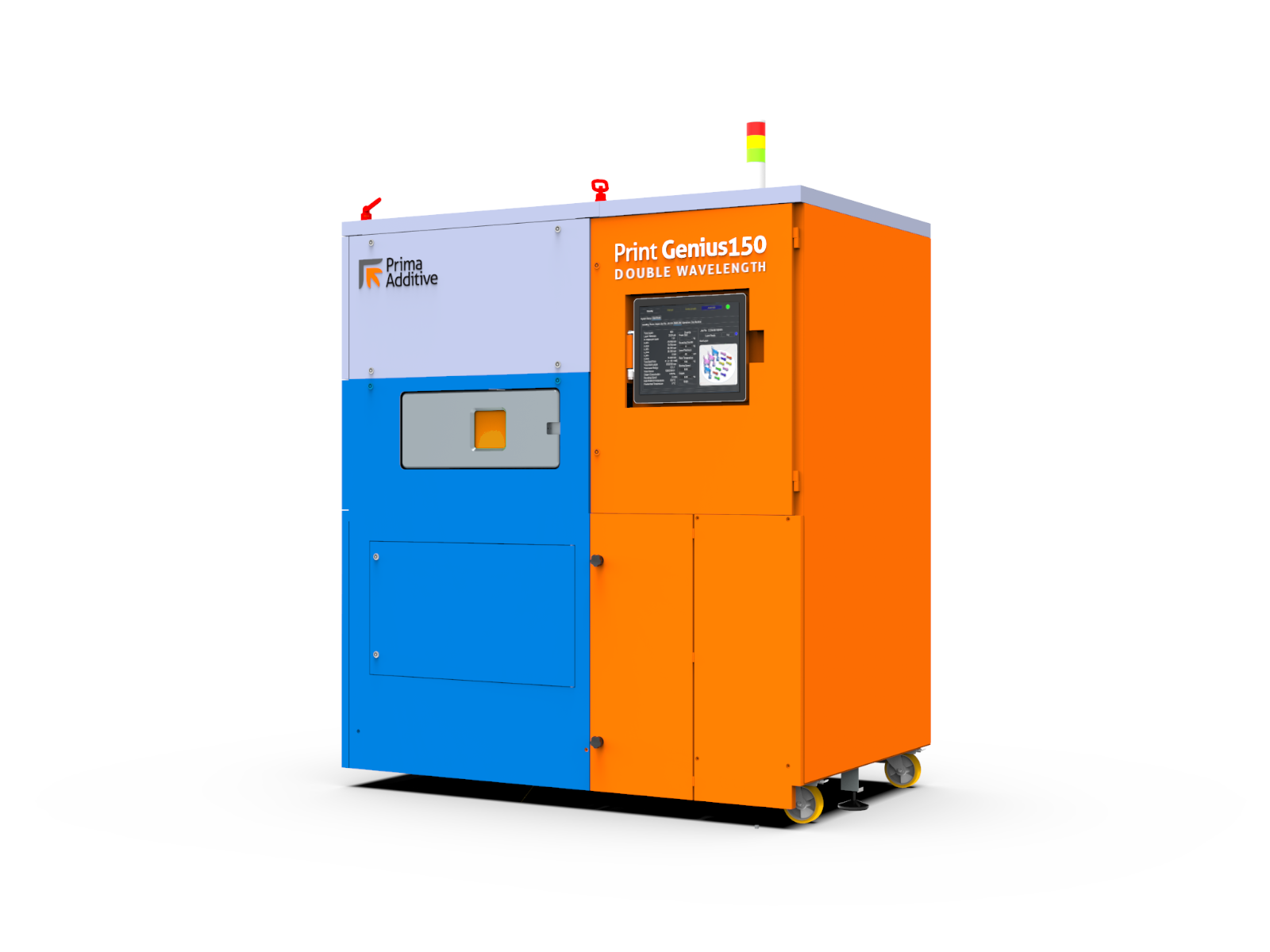
For Direct Energy Deposition technology, at the Prima Additive’s booth it will be possible to see the IANUS multiprocess robotic cell at work, which also features an innovative laser configuration. In fact, it will be equipped with a 3kw blue laser. The special feature of this different laser implementation is the ability to process highly reflective materials, ensuring excellent and efficient results. Also, the versatility of the IANUS cell allows the machine to be equipped with two different laser sources within the same system, and changing sources as needed on the same laser head.
The IANUS cell, with a working area of 1600 x 1200 x 700 mm and a build volume of 1440 x 850 x 540 mm, can be configured for different laser processes. Actually, in addition to the direct deposition head based on metal powder, it is possible to configure the machine for Direct Energy Deposition based on the use of metal wire, or other laser processes such as remote welding and laser hardening. In line with the flexible applications offered by Prima Additive, the innovative cell is also available in a Double Wavelength version, with infrared and blue laser.
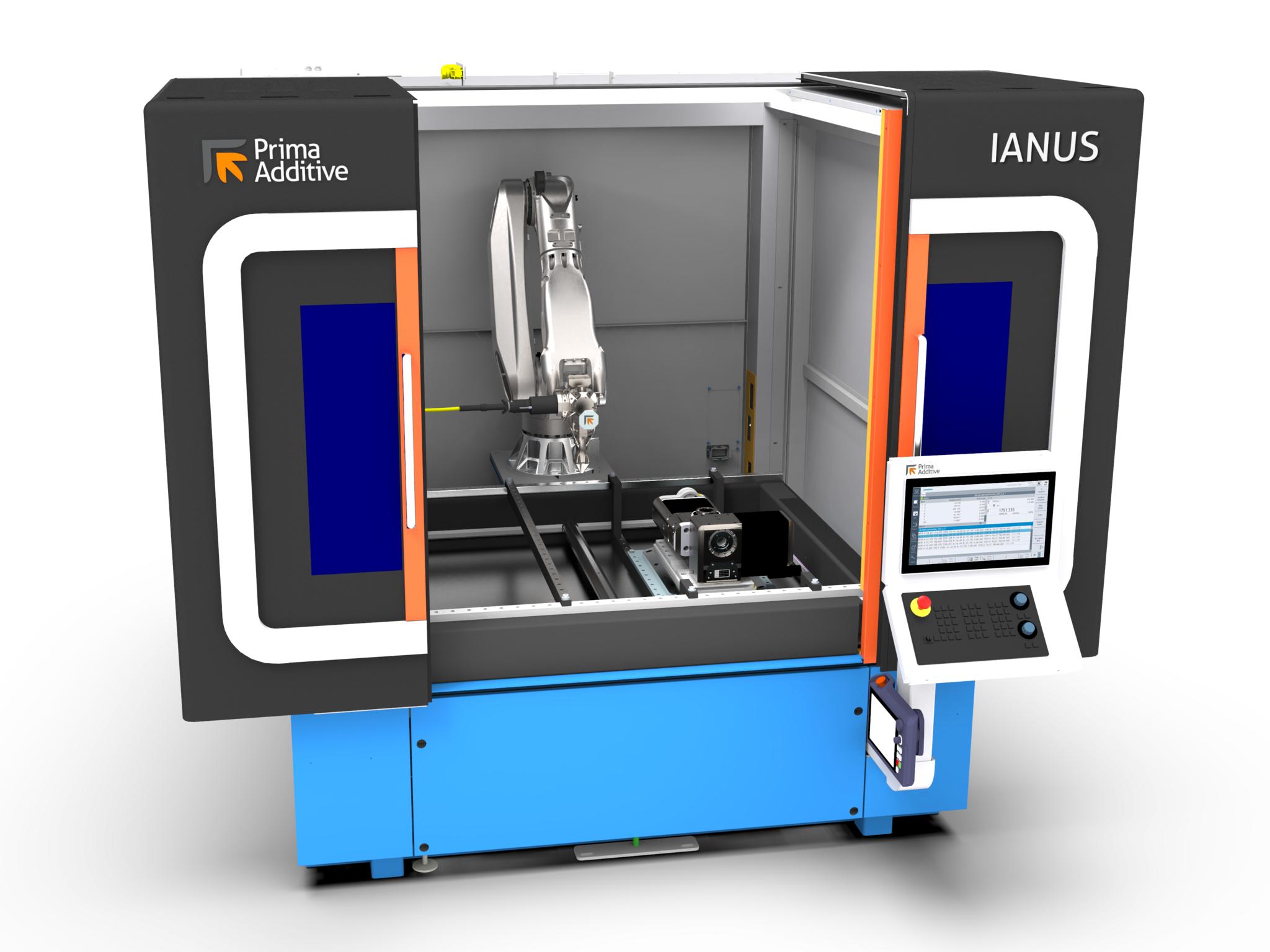
This system presents a series of functional solutions for its inclusion in the factory of the future. For this reason, it was developed by Prima Additive in collaboration with Siemens, a leading company in automation and digitalization with specific skills in the field of robotics and additive manufacturing. The integration between the technologies of Siemens and those of Prima Additive is expressed, first of all, through the integration of the robotic arm and the CNC, through the Sinumerik Run MyRobot / Direct Control functionality.
Through this functionality, the user of the machine will be able to interface with the robotic cell using a single control console but above all, he will be able to carry out the movement and programming of the robot using typical instructions of a machine tool, thus exempting him from knowing an additional programming language specific for robots. The integrated use of the CAD-CAM-CNC chain, made possible using the NX platform and the Sinumerik One numerical control, is completed by the integration of digital solutions and data management.
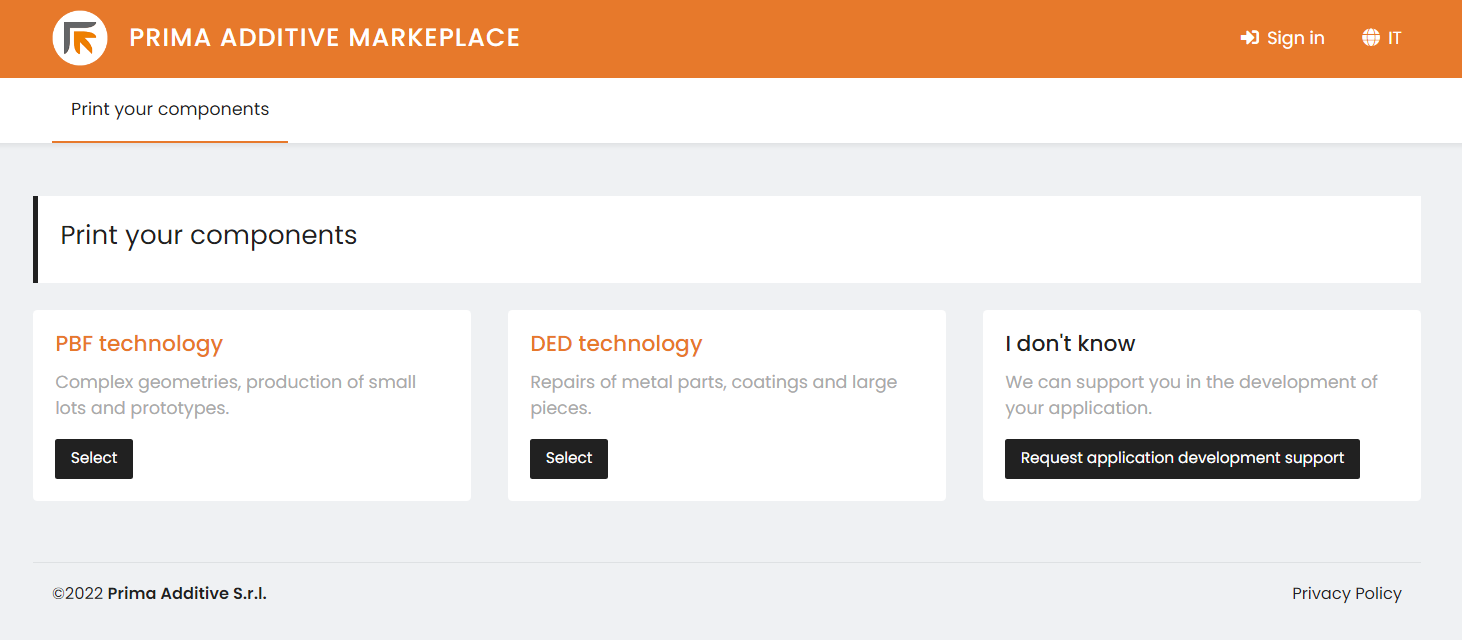
Prima Additive provides not only machines but also digital services which will be given ample space during the Formnext fair. Above all, the "Prima Additive Marketplace" represents one of the efforts of the Italian company in the direction of reducing the barriers to entry of metal additive manufacturing, while making production increasingly digitized. Through this platform, accessible at https://marketplace.primaadditive.com and created in collaboration with Morphica, the innovative Italian SME that provides 3D printing services, it will be possible to request the creation of metal components, starting from a 3D file.
The Prima Additive Marketplace leverages the production capacity of Prima Open Additive Labs, the network of companies, universities, and research centers that provide support on additive manufacturing, and Prima Additive customers to provide an on-demand production service, which can make the metal additive manufacturing accessible even to companies that do not have the possibility or the volumes necessary to have their own system.
In addition to the possibility of directly requesting the printing of the component, on this digital platform it is also possible to obtain dedicated consultancy, functional to the realization of an application study, with which to explore the potential of additive manufacturing on the specific case of the customer, analyzing the opportunities for engineering of its component and identifying the main advantages and possible criticalities.
Do you want to come and visit us at Formnext? Request a free ticket: