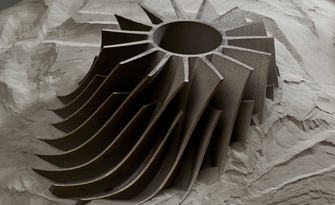
Solutions that fit your needs
At Prima Additive, we understand that production needs vary greatly from one company to another. Each company has specific production goals, which may depend on the type of materials to be processed, the production volume or the size of the parts to be produced.
To meet these different needs, we have developed a design philosophy based on the flexibility and customization of our machines. Thanks to our ability to combine different Powder Bed Fusion machine platforms with variable laser configurations – from 1 to 4 lasers, available in infrared or green versions – we offer solutions that perfectly adapt to the customer's needs. The selection of the platform depends mainly on the size of the components to be produced, while the laser configuration is chosen based on the materials to be processed and the desired annual production. This modularity allows our customers to get the most out of their production processes, increasing efficiency and competitiveness.
Whether you need to improve production speed, work with complex materials or achieve precise geometries, our tailor-made solutions offer the right balance of productivity and versatility, ensuring that every project is realized with the highest quality and precision.
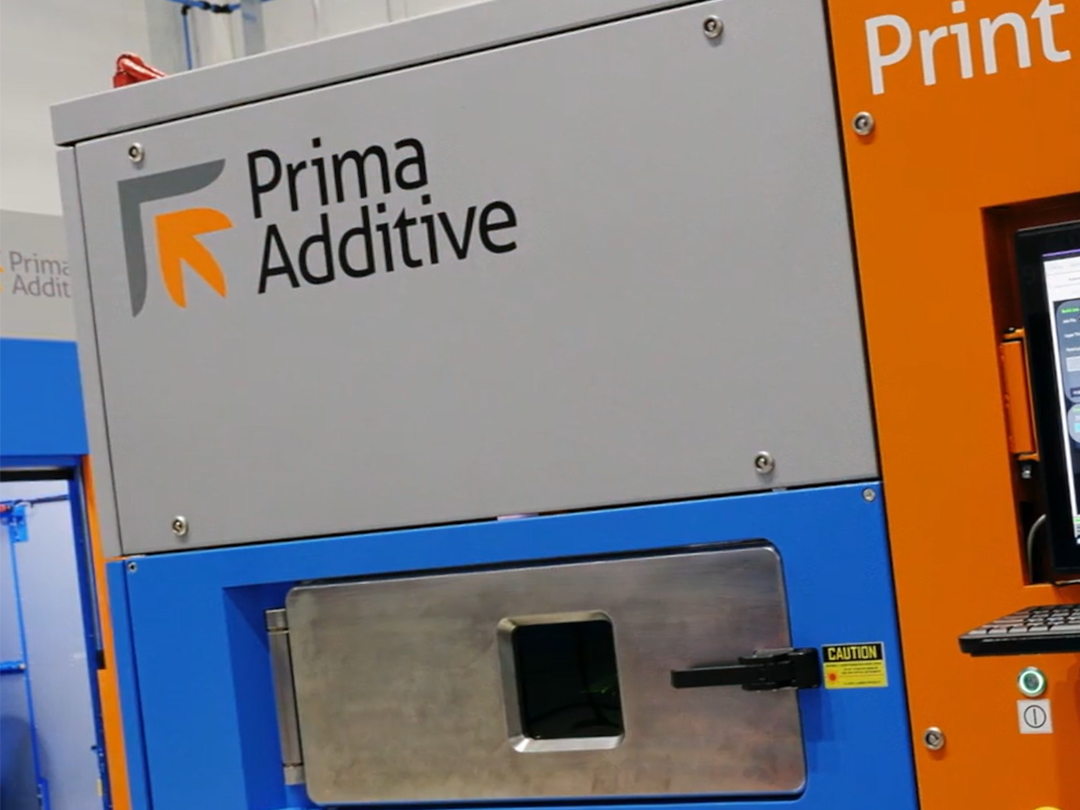
Combining Platforms and Laser Configurations for Optimal Solutions
Prima Additive stands at the forefront of the additive manufacturing industry, renowned for its innovative solutions that revolutionize traditional manufacturing methods. By leveraging advanced technologies, Prima Additive offers highly customized and efficient manufacturing solutions tailored to meet the unique needs of various industries. Their approach is grounded in a commitment to innovation, quality, and customer satisfaction, ensuring that every product delivered represents state-of-the-art technology.
At the core of Prima Additive's offerings is the Powder Bed Fusion technology, a process that involves selectively melting and fusing powdered material using a high-energy laser beam, layer by layer, to create intricate and precise components. This technology allows for the production of complex geometries and detailed structures that would be challenging or impossible to achieve with traditional manufacturing methods. Powder Bed Fusion technology's precision and flexibility make it ideal for aerospace, automotive, medical, and other high-tech industries.
For these reasons, Prima Additive provides a wide range of machine platforms specifically designed for Powder Bed Fusion. They include advanced features that enable seamless integration with various laser configurations, ensuring optimal performance and a high degree of versatility for coping with different manufacturing needs. Moreover, the modular design of these platforms allows for easy upgrades and customization, catering to the evolving demands of the industry.
Another standout feature of Prima Additive's Powder Bed Fusion platforms is the ability to integrate various laser configurations, each designed to enhance specific aspects of the manufacturing process. The multi-laser configuration is a prime example, significantly boosting productivity by allowing multiple lasers to operate simultaneously. This setup reduces build times and increases throughput, making it ideal for high-volume production runs.
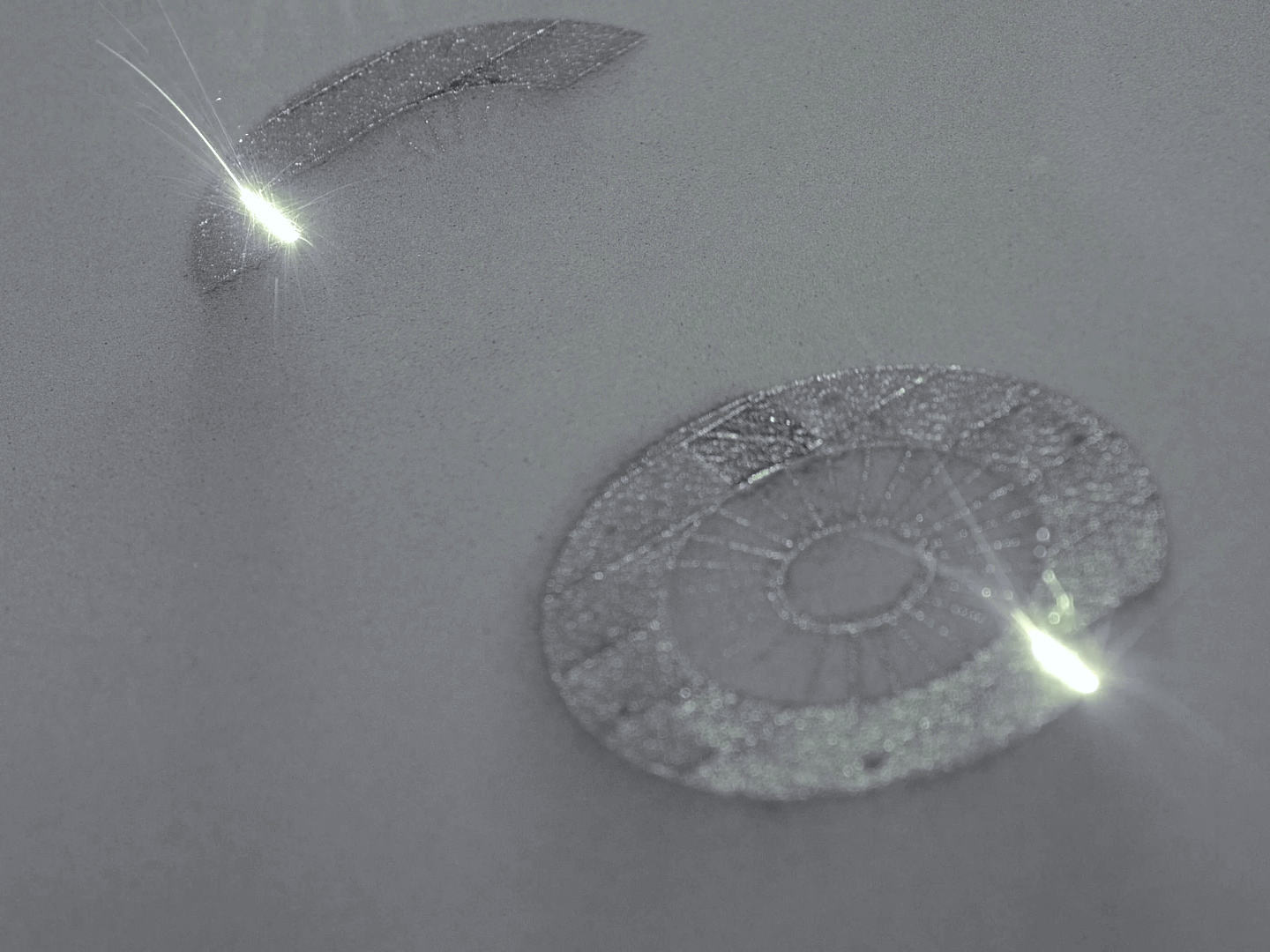
High Productivity and Material Versatility with Multi-Laser Technology
The introduction of multi-laser configurations in additive manufacturing has revolutionized the productivity and efficiency of production processes. Prima Additive has been at the forefront of this innovation, utilizing multi-laser technology to significantly boost productivity. By employing multiple laser sources simultaneously, Prima Additive's machines can dramatically reduce build times and increase throughput.
In effect, with multiple lasers working concurrently, larger areas of the powder bed can be processed simultaneously, which accelerates the overall production process. The precision that can be achieved with Prima Additive additive manufacturing systems is essential in sectors such as aerospace and automotive, where component accuracy and integrity are paramount.
Prima Additive's innovative approach includes the use of various types of lasers, combining the green laser with traditional infrared lasers, to improve the versatility of the materials:
Green laser technology is highly useful when handling reflective materials such as pure copper, copper alloys, gold, and other precious metals. Traditional infrared lasers often struggle with these materials due to their high reflectivity, leading to inefficient melting and poor-quality outputs. Green lasers, instead, with their superior absorption rates, overcome these challenges, ensuring efficient and repeatable processing of reflective metals.
The ability to choose from different laser types allows manufacturers in many different industries to tailor their production processes to the specific needs of each project, ensuring optimal results. In this way, with Prima Additive’s customized solutions, our customers can achieve a significant competitive advantage and allow their businesses to grow over time.
Prima Additive's flexible approach to laser configurations does meet a wide range of different customer needs. For instance, customers requiring high productivity can benefit from the multi-laser configuration, which significantly reduces production time. Those needing to work with reflective materials like copper can utilize the green laser configuration for optimal results. Additionally, the combination of infrared and green lasers can be employed to handle a variety of materials, providing a versatile solution for complex manufacturing requirements.
Prima Additive platforms can be configured with one to four lasers, with the option to choose between infrared and green. The smallest platform, called Print 150, with a working area of Ø 150 x 160 mm, can be configured with a single infrared or green laser, or with two lasers, which can be both infrared, both green or in a double wavelength configuration with one infrared and one green in the same system. The same configurations are also available on the Print 300 platform (working volume 330 x 330 x 400 mm), which is also available with quad laser configurations, with four infrared or green lasers. Finally, the two and four laser configurations mentioned above are also available on the largest platform, the Print 400, equipped with a working area of 430 x 430 x 600 mm or 430 x 430 x 1000 mm in the XL version.
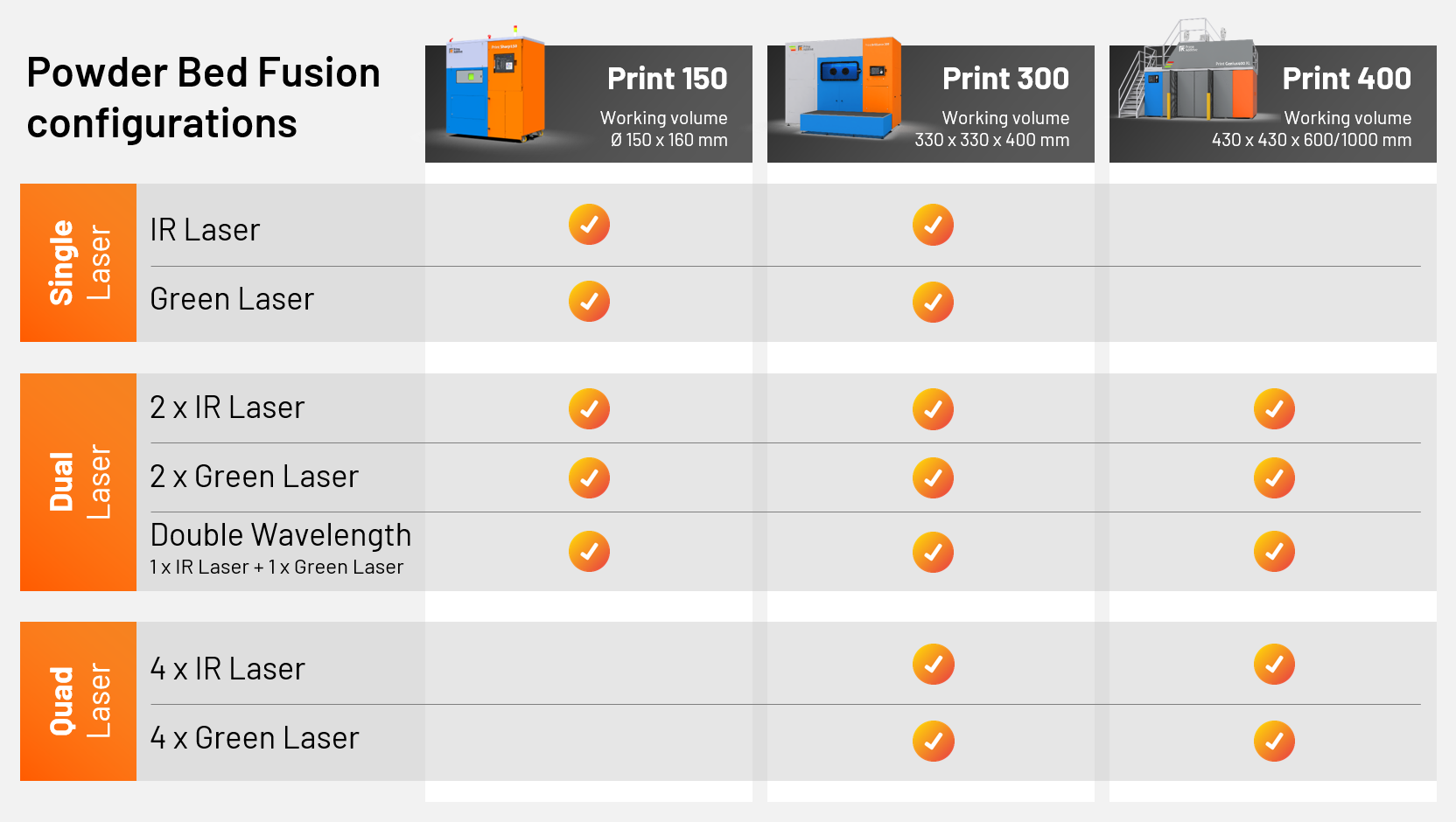
Tailored Additive Manufacturing Solutions for Every Industry
Prima Additive's commitment to providing tailored additive manufacturing solutions has positioned it as a leading partner for companies operating in various industries including aerospace, automotive, and electronics, among others.
In the aerospace industry, precision and lightweight components are critical. Prima Additive's Powder Bed Fusion technology enables the production of complex geometries and high-strength parts that are essential for aerospace applications. For instance, components such as turbine blades and other structural parts can be manufactured with minimal weight while maintaining structural integrity. The ability to create intricate internal structures also allows for improved thermal management, which is crucial in aerospace engineering.
Also the automotive industry benefits significantly from Prima Additive's multi-laser configurations. High productivity and efficiency are vital for automotive manufacturers, and the use of multiple lasers ensures faster production times without compromising quality. Customized applications in this sector include lightweight engine parts, exhaust systems, and custom-designed interior components. These parts can be produced quickly and accurately, reducing time to market and enabling manufacturers to stay competitive.
In the electronics industry, the need for precise and intricate designs is paramount. Green laser technology offered by Prima Additive is particularly effective for producing small, detailed components such as connectors, housings, and heat sinks. The ability to work with reflective materials like copper ensures that electronic components have optimal thermal and electrical conductivity. This precision and versatility enable the production of high-performance electronic devices that meet stringent industry standards.
In every industry, Prima Additive’s approach goes beyond simply providing advanced manufacturing technology. It all starts with the application assessment and only after all the business case assessments and application validation are carried out, the most suitable machine platform and laser configuration for each project is identified. But the partnership does not end with the delivery of the equipment: Prima Additive provides ongoing support and consultancy to ensure that the chosen solution continues to meet the customer’s needs. This includes training, maintenance and upgrades to keep the production process efficient and up to date.
Businesses seeking to innovate and enhance their manufacturing capabilities are encouraged to explore Prima Additive’s advanced solutions. Whether you are in aerospace, automotive, electronics, or any other industry, Prima Additive's tailored additive manufacturing solutions can help you achieve your production goals with precision and efficiency. Contact Prima Additive today to discover how our expertise and cutting-edge technology can revolutionize your manufacturing processes and drive your business forward.
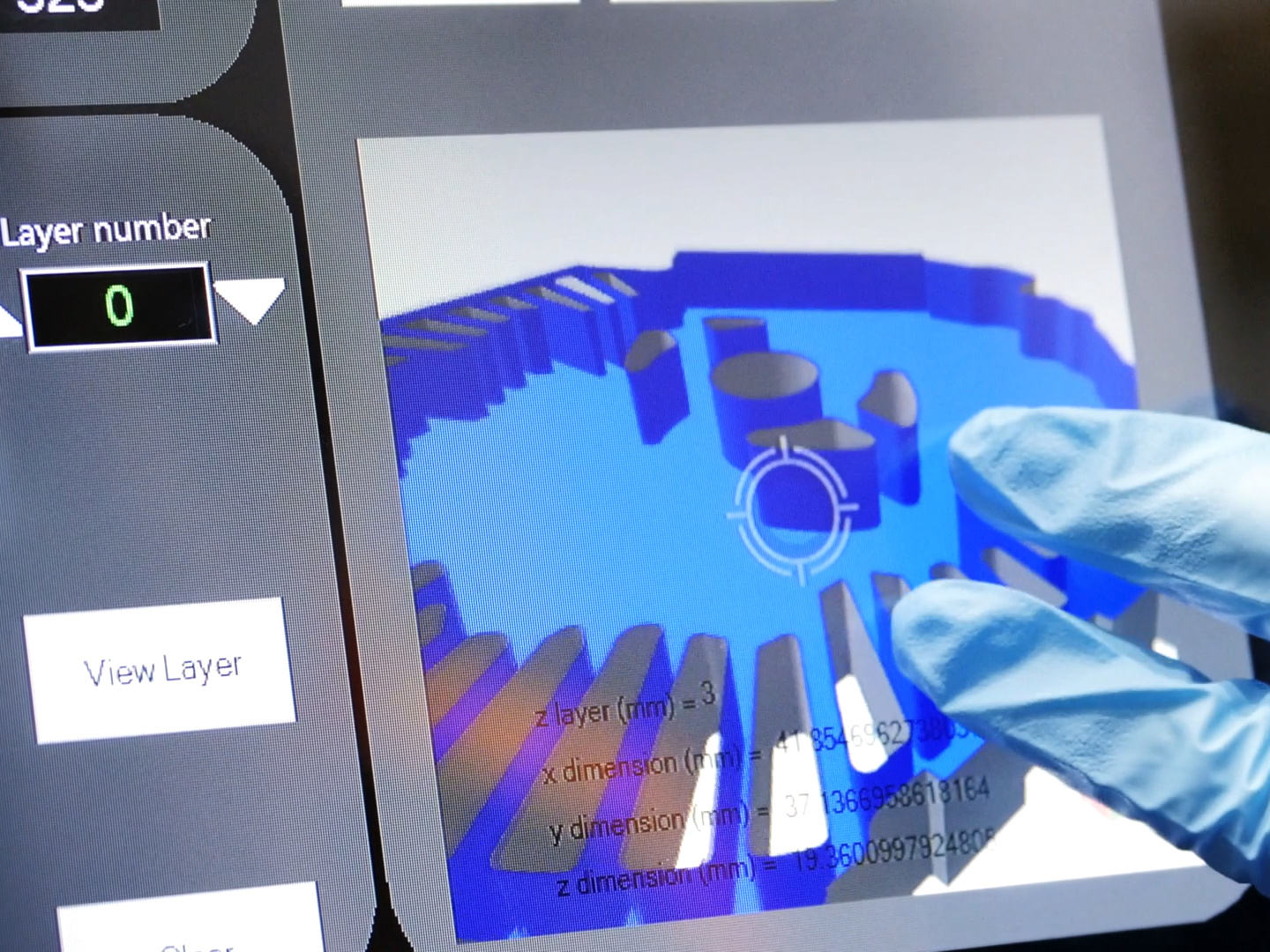