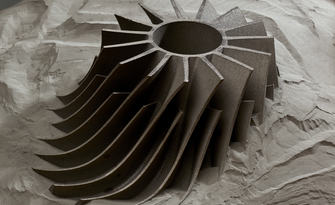
Laser melting for the dental industry
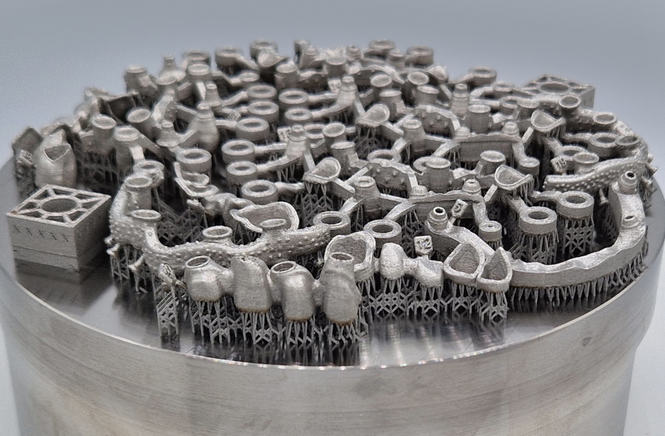
The flexibility and precision of metal additive manufacturing prove to be particularly functional when it comes to creating highly customized components, as occurs in the dental field.
The flexibility and precision of metal additive manufacturing prove to be particularly functional when it comes to creating highly customized components, as occurs in the dental field.
In particular, Additive Manufacturing has already established itself for some years as the prevailing technique in the dental technology field, where it is mostly known as "laser melting", for the production of prostheses, crowns, partial frames, and bridges.
In this industry, the needs of patients are always different: since no two people have the same teeth or gums, consequently there cannot be two identical prostheses.
Among the most used materials in this field, there are above all titanium and cobalt-chrome, chosen for their characteristics of biocompatibility and resistance to corrosion.
In this sector Prima Additive is establishing itself thanks to its solutions from the Print 150 family. Available in the single laser version (Print Sharp 150) or double laser (Print Genius 150), with a working volume of Ø 150 x 160 mm represents an optimal solution for this sector, with the possibility of creating up to 180 elements with a single print job lasting just over three hours.
In this way, the time between the design and the finished product is drastically shortened. All with a process that improves the accuracy of the prosthesis, thanks to a 50 µm laser spot, which guarantees very high dimensional and detail precision on all corners, spaces, and edges, without any breakage problems.
Furthermore, the laser melting is a particularly sustainable process: in fact, the unused material can be recovered and recycled instantly.
Among the companies that have chosen a Prima Additive system, and which today support the Turin-based company in the development of optimized solutions for the dental industry, is 8853 S.p.A. through its 88dent business unit.
8853 S.p.A., an Italian company specializing in the trading of precious metals, has been working in the dental world for almost 50 years. The activity has evolved over time, starting from the production of dental alloys, up to developing a dedicated Business Unit entirely focused on the dental sector (88dent) with two lines: one designed for dental laboratories and one for dental practices.
88dent CLINICAL provides the dentist with the latest generation technologies such as diode lasers, intraoral scanners, software, and machinery. 88Dent LAB allows dental technicians to digitize themselves, maintaining the aesthetic customization that has always characterized their profession.
The two lines make it possible to improve the work and communication between dentists, dental technicians, and patients, for a solution that brings advantages to the everyday work of these figures.
As far as additive technologies are concerned, they have arrived in the dental world for a couple of decades now and guarantee a level of precision and productivity of the highest level.
8853 S.p.A. with the BU 88Dent was a pioneer in this specific sector, first through important collaborations and now it proposes itself directly as a manufacturer in partnership with Prima Additive with the Print Genius 150.
The Print Genius 150 is a solution that the Prima Additive experts have studied to meet the specific needs of the dental industry and thanks to the additive technique it is possible to shorten the time needed to create restorations and dental structures, reducing costs and increasing work.
Additive manufacturing is the natural conclusion of a digital workflow that 88dent offers to its customers all over the world, whether they are small laboratories that can rely on the external production service (outsourcing) or large production centers that can take advantage of the 88dent in proposing specific solutions for your needs.
Through a dedicated portal available on the 88dent.com website, the customer can upload the file (or several files) of the prosthesis to be created with just a few clicks and within 24/48 hours can receive the semi-finished product or the structure to be finalized.
The customer can count on an open system that goes from scanning the dental model to designing using dedicated CAD software, with technical assistance and specific ongoing training.
Additive manufacturing technology stands out for its speed of realization, cost-effectiveness, and technical possibilities that other technologies such as subtractive ones do not possess. Even waste compared to subtractive technologies is almost eliminated, with unrivaled cost-effectiveness and sustainability.
88dent, a pioneer in the search for specific solutions in the dental field, already offers prosthetic structures made with hybrid techniques in order to best combine the worlds of additive and milling. Today it gives its customers the possibility to produce a varied range of processes such as crowns, bridges, implant bars, torontos, customized abutments, splints, skeletons, cobalt-chrome, or titanium reinforcing meshes.
The development of new solutions dedicated to the dental industry will continue in the coming years with an increasingly active collaboration between Prima Additive and 88dent because it is precisely when the skills of the machine manufacturers join those of those who use them daily that it is possible to optimize turnkey solutions.
Application support
Open innovation
Circular economy inspired
© Prima Additive S.r.l. | Corso Re Umberto, 54 - 10128 Torino (TO) Italia | Share Capital € 116.860,77 fully paid up | VAT 11434740012 - C.C.I.A.A.Torino 1213183 | Reg. Impr. Torino n. 11434740012