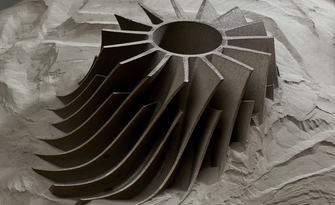
Gli anni 2020, per quanto visto finora, mettono il mondo di fronte ad alcune sfide, la cui soluzione sarà di cruciale importanza per il futuro. In primo luogo, c’è la situazione pandemica, che ha riportato ognuno di noi a ripensare alla propria vita e, più nello specifico, ha portato le aziende a riconsiderare le proprie priorità: le difficoltà negli spostamenti e i rallentamenti nella produzione mondiale hanno generato una supply chain globale sempre più frammentata e sempre meno affidabile. In secondo luogo, il costo delle materie prime e dell’energia è lievitato enormemente, con un conseguente aumento dei costi di produzione e delle incertezze in ogni mercato. Come terzo aspetto, probabilmente ancora più importante dei primi due, c’è la questione dei cambiamenti climatici: un fenomeno ormai avviato e innegabile, che potrebbe generare sconvolgimenti ancora più grandi di quelli a cui abbiamo assistito negli ultimi due anni.
Di fronte a queste sfide, tutti noi come individui, ma in particolar modo le aziende manifatturiere, siamo chiamati ad agire, cercando una soluzione per fronteggiarle e per fare la propria parte nella loro soluzione, fornendo ai nostri clienti soluzioni in grado di rafforzare la loro competitività, migliorandone la produttività, la flessibilità e l’efficienza.

Dal punto di vista di Prima Additive, in qualità di fornitori di sistemi industriali, il nostro ruolo è quello di fornire a chi produce i giusti strumenti per affrontare le incertezze di questi tempi. L’additive manufacturing del metallo, infatti, offre risposte concrete ai tre problemi citati rivoluzionando l’approccio al componente, dalla sua progettazione alla sua realizzazione, permettendo così di concepire nuovi modelli di business e partecipando a rendere la produzione più sostenibile.
In primo luogo, questa tecnologia abilita la cosiddetta “produzione on-demand”: ovvero la possibilità di realizzare parti complesse in metallo, producendo solo ciò che serve, quando serve e dove serve. Così facendo, è possibile ridurre la disponibilità del magazzino, riducendo l’impatto che questo ha su consumi e costi di gestione. Inoltre, si riducono i consumi e i costi di logistica per trasportare i pezzi da un’area del mondo ad un’altra e, infine, si ottimizza la catena di approvvigionamento, mettendola al riparo da ogni tipo di rallentamento generato da una supply chain globale sempre più frammentata e sempre meno affidabile. Internalizzando la realizzazione di molti pezzi grazie all’additive manufacturing, il re-shoring della propria produzione diventa quindi semplice e si riduce il numero di step necessari per realizzare il pezzo finito.
Dal punto di vista della riduzione degli sprechi di materiale, nonché della crescente difficoltà nel reperire le materie prime e del loro costo in continua crescita, l’additive manufacturing è un grande alleato poiché consente di limitare l’utilizzo del materiale alla sola quantità necessaria per realizzare il pezzo. Le polveri di metallo utilizzate nel processo additivo, possono poi essere riciclate, permettendo un approccio favorevole alla riduzione degli scarti e più sostenibile rispetto al processo di asportazione che implica una grande percentuale di scarti e un processo lungo di recupero degli stessi. Il riciclo delle polveri inutilizzate nel processo additivo avviene istantaneamente e autonomamente, con la possibilità di riutilizzare le polveri per diversi cicli di produzione.
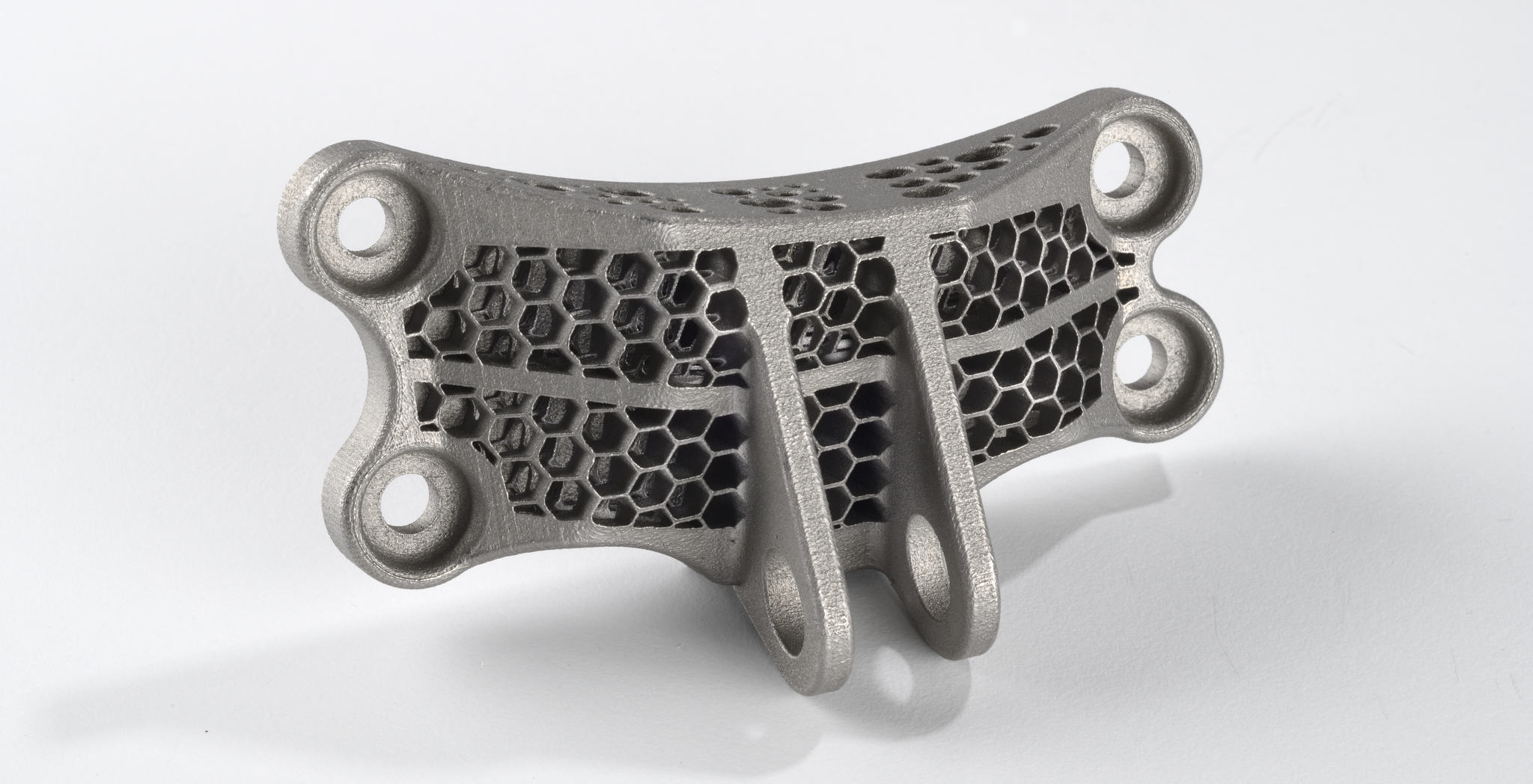
La sostenibilità dell’Additive Manufacturing si evidenzia anche sul prodotto, che può essere realizzato con geometrie ottimizzate, rendendolo più leggero, a parità di funzionalità e di caratteristiche meccaniche.
Questo è possibile anche perché l’additive manufacturing non si limita alla fase di produzione di un componente, ma raggiunge il massimo delle sue potenzialità quando coinvolge ragionamenti su ciò che viene prima e ciò che viene dopo la produzione, ovvero la progettazione e lo smaltimento. Innanzitutto, le grandi opportunità offerte da questa tecnologia aprono moltissime strade nell’ambito del design: una progettazione efficiente di un pezzo è quella che non considera soltanto la produzione e l’utilizzo dello stesso, ma anche cosa accadrà quando dovrà essere smaltito. Disporre di una tecnologia così versatile aiuta a ridurre gli assemblaggi, ma anche il numero di materiali diversi utilizzati: in questo modo, quando il componente raggiungerà la fine del suo ciclo di vita, sarà più semplice il suo smaltimento. Inoltre, i pezzi progettati tenendo conto del loro utilizzo, sono “green” negli effetti che possono generare durante il loro utilizzo. Parlando di un settore che per primo ha creduto in questa tecnologia come l’aerospace, ad esempio, l’adozione di pezzi realizzati in additive non costituisce soltanto un vantaggio in termini di funzionalità del velivolo, ma rappresenta anche un reale elemento di rispetto dell’ambiente e della sostenibilità del business aerospaziale. Ridurre il peso di un aereo consente allo stesso tempo di ridurre il consumo di carburante del velivolo e, di conseguenza, ridurre le sue emissioni di CO2 nell’atmosfera. Lo stesso vale per il settore dell’automotive, dove l’elettrificazione dei veicoli porta verso veicoli sempre più pesanti: la sfida dei prossimi anni starà nel loro alleggerimento al fine di aumentarne l’efficienza e, siamo sicuri, l’additive giocherà un ruolo cruciale in questa sfida.
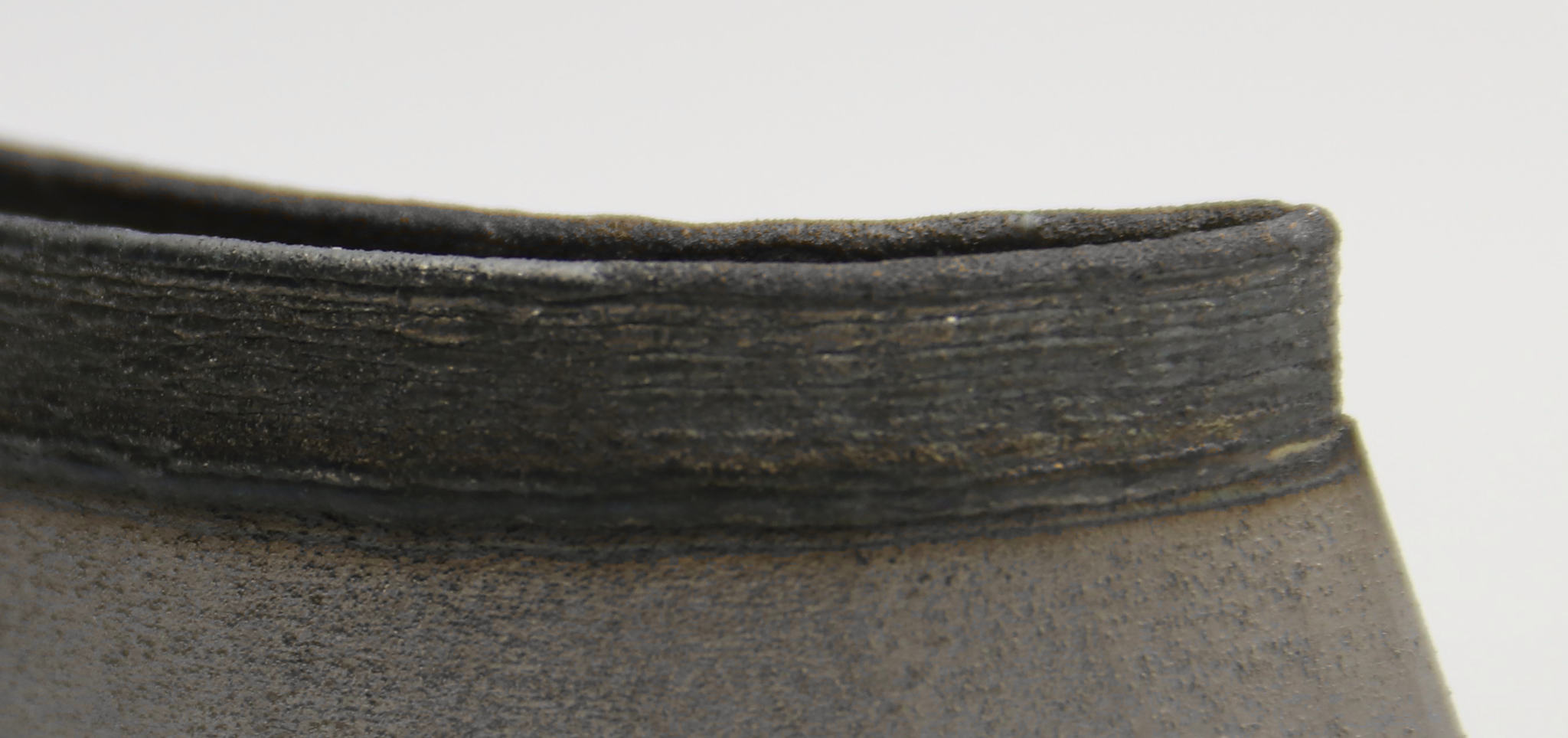
Oltre all’alleggerimento dei prodotti, è importante poter lavorare su concetti di funzionalizzazione dei componenti o di riparazione degli stessi. In quest’ottica Prima Additive non si limita a fornire soluzioni con tecnologia di Powder Bed Fusion, utile a produrre pezzi finiti, ma è anche attiva con la tecnologia Direct Energy Deposition, proponendo sistemi che si collocano perfettamente all’interno di un’idea di sostenibilità industriale e di economia circolare, consentendo di riparare o funzionalizzare parti in metallo: un componente, quando è troppo usurato, può essere riparato in poche ore, allungando così il suo ciclo di vita ed evitando ulteriore utilizzo di risorse ed energia per crearne uno nuovo.
Tutti questi temi mostrano come l’additive manufacturing del metallo possa contribuire attivamente ad un approccio più sostenibile e l’obiettivo di Prima Additive di rendere questa tecnologia sempre più competitiva, così da permettere all’utilizzatore finale di adottare una soluzione profittevole per fronteggiare le sfide dei nostri tempi.
Questo obiettivo è perseguito da Prima Additive attraverso la realizzazione di nuovi concept di sistemi, lo sviluppo di un processo affidabile per diverse applicazioni e materiali, il pieno supporto al cliente per adottare tale tecnologia. Questo è possibile anche perché Prima Additive fa parte del Gruppo Prima Industrie, che ha una storia di innovazione tecnologica nel settore industriale del manifatturiero. Il nostro DNA di innovatori nel campo della meccatronica, della fotonica e dell’innovazione di processo, ci permetterà di realizzare sistemi sempre più performanti, più produttivi e più automatizzati, con l’obbiettivo di soddisfare le esigenze dei nostri clienti e sostenerli in un ambiente che è sempre più interconnesso, agile, dinamico.