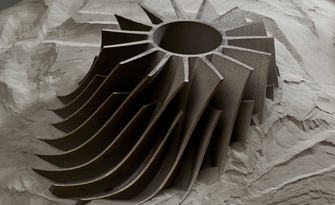
Produzione di energia sostenibile: il ruolo dell’additive manufacturing
Nel mondo di oggi, in cui la domanda di energia continua a salire, l'imperativo di produrre abbondanti quantità di energia con il minimo impatto ambientale è fondamentale. Lo sviluppo di fonti a zero emissioni di carbonio come l'energia eolica, solare, geotermica, idroelettrica e nucleare segna un passo significativo verso questo obiettivo. Queste fonti mitigano gli effetti del cambiamento climatico e offrono un'alternativa sostenibile ai combustibili fossili tradizionali.
L’Additive Manufacturing svolge un ruolo trasformativo nella produzione di componenti per la produzione di energia sostenibile. Come processo di produzione, la manifattura additiva è intrinsecamente sostenibile, riducendo al minimo gli sprechi e utilizzando solo il materiale necessario strato per strato per creare strutture complesse. Questo metodo contrasta con la tradizionale produzione sottrattiva, dove il recupero del materiale inutilizzato non è un processo immediato. La capacità della produzione additiva di produrre componenti on-demand ne migliora ulteriormente la sostenibilità, riducendo la necessità di grandi scorte e lunghe catene di approvvigionamento.
La sostenibilità dell’additive manufacturing va oltre il semplice processo. Infatti, consente di produrre in maniera conveniente componenti complessi essenziali nei sistemi di energia rinnovabile, come intricate parti per le turbine delle pale eoliche o componenti complessi in materiali non convenzionali per impianti fotovoltaici. Questi componenti, spesso difficili e costosi da produrre in modo convenzionale, possono essere prodotti in modo più efficiente con la produzione additiva. Le migliori performance raggiunte si rivelano quindi fondamentali per accelerare l’adozione delle tecnologie legate alle energie rinnovabili, rendendole più accessibili ed economicamente sostenibili.
Inoltre, l’impatto dell’additive manufacturing del metallo non si limita ai settori delle energie rinnovabili. Nei settori energetici tradizionali, come quello dell’Oil & Gas, la produzione additiva offre vantaggi sostanziali. Consentendo la produzione in loco di componenti e la riparazione efficiente delle parti esistenti attraverso tecnologie come la Direct Energy Deposition, la produzione additiva può ridurre significativamente i tempi di inattività e i costi operativi. Questo aspetto è particolarmente vantaggioso nelle piattaforme offshore o nei siti di perforazione remoti, dove l'attesa dei pezzi di ricambio può essere costosa. Inoltre, riparando e riutilizzando i componenti, l’additive manufacturing contribuisce a un’economia più circolare, riducendo l’impatto ambientale anche nei settori tradizionalmente ad alte emissioni.
In conclusione, l'Additive Manufacturing emerge non solo come strumento per l'efficienza produttiva ma come vero e proprio catalizzatore per una transizione energetica sostenibile. Che si tratti di ridurre i costi dei componenti per la produzione di energia rinnovabile o di migliorare l'efficienza dei settori energetici tradizionali, la produzione additiva è in prima linea nell'innovazione industriale sostenibile. Il suo ruolo nel plasmare un futuro più green e sostenibile per la produzione di energia è indiscutibile, segnando un significativo passo avanti nel viaggio verso la transizione energetica e la resilienza climatica.
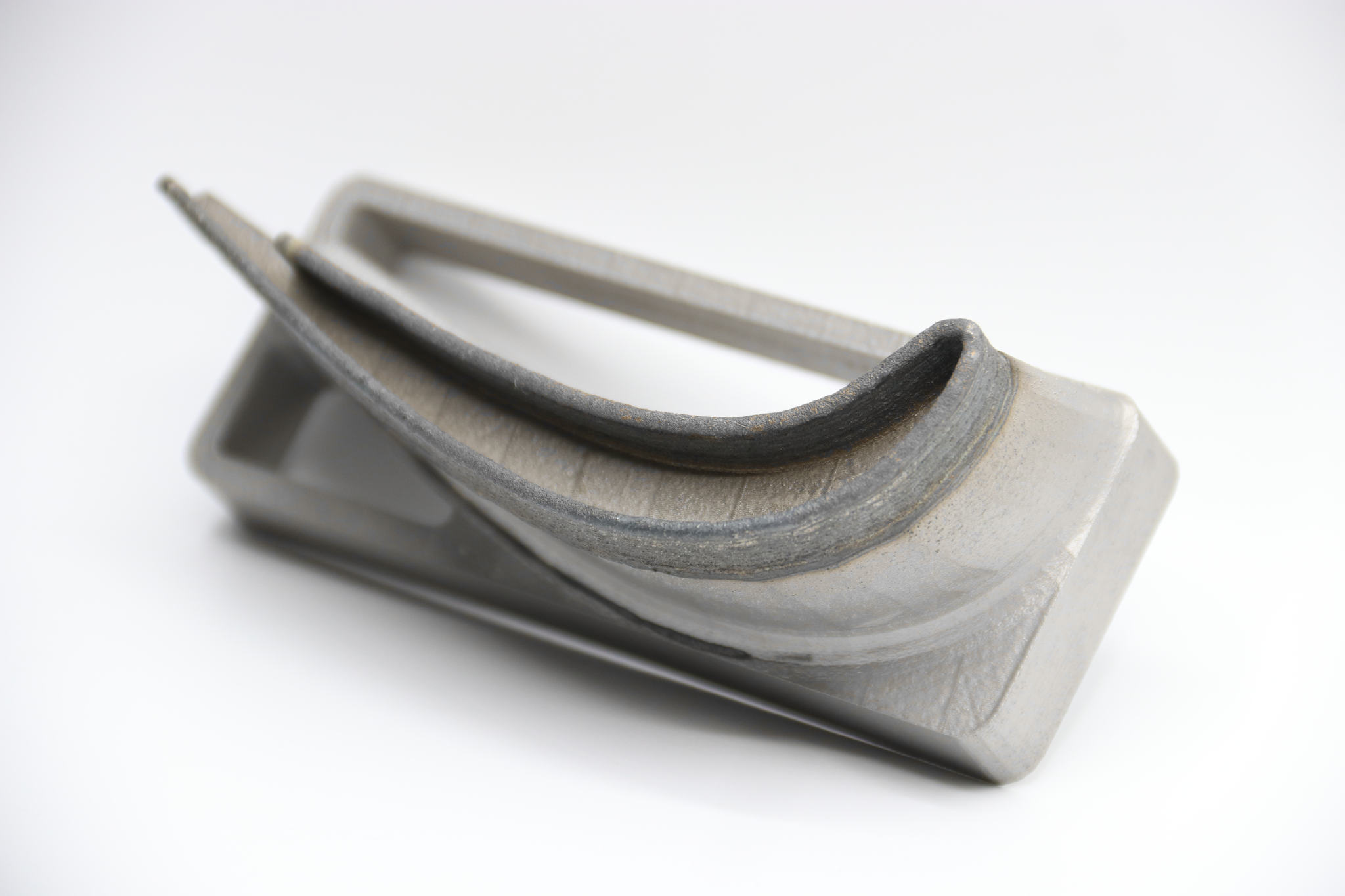
Rivoluzionare la produzione di energia con tecnologie additive avanzate
Il lavoro pionieristico di Prima Additive nel settore energetico mostra l'immenso potenziale delle tecnologie di additive manufacturing del metallo. In qualità di uno dei principali attori del settore, Prima Additive si concentra su due processi tecnologici chiave basati sull’uso di laser: la Powder Bed Fusion e la Direct Energy Deposition. Queste tecnologie stanno ridefinendo il numero di componenti per la produzione di energia che possono essere creati o rigenerati, offrendo vantaggi significativi rispetto ai metodi di produzione tradizionali.
Quello della Powder Bed Fusion è un sofisticato processo di produzione additiva utilizzato da Prima Additive, che prevede la stesura di un sottile strato di polvere metallica che viene fuso selettivamente utilizzando un laser, sulla base di un modello digitale. Questo metodo è particolarmente adatto per la produzione di geometrie complesse e design intricati che sarebbero impegnativi o impossibili con la produzione convenzionale. La Powder Bed Fusion eccelle nella creazione di parti ad alta risoluzione e di alta qualità per qualsiasi applicazione energetica, come componenti di precisione per turbine eoliche o parti complesse per impianti termoelettrici tradizionali. Il vantaggio principale della Powder Bed Fusion risiede nella sua capacità di produrre componenti leggeri ma resistenti, fondamentali per migliorare l'efficienza e le prestazioni dei sistemi di energia rinnovabile.
La Directed Energy Deposition, anche conosciuta come Laser Metal Deposition, è un altro processo innovativo impiegato da Prima Additive, che offre immensi vantaggi, soprattutto nella riparazione e nell'aggiunta di materiale ai componenti esistenti. La tecnologia di deposizione diretta di energia funziona fondendo polvere di metallo o filo metallico in una pozza fusa creata da un laser. Questo metodo è particolarmente efficace per la riparazione di componenti ad alto valore aggiunto come pale di turbine o giranti, prolungandone la durata e riducendo gli sprechi. Il processo di Direct Energy Deposition non è solo economico, ma anche rispettoso dell'ambiente, in quanto riduce la necessità di nuove materie prime e riduce al minimo gli sprechi. La tecnologia Direct Energy Deposition di Prima Additive è un punto di svolta per il settore energetico, in particolare per quanto riguarda il mantenimento e l'ottimizzazione delle prestazioni delle infrastrutture energetiche esistenti.
Queste tecnologie avanzate di Prima Additive offrono numerosi vantaggi rispetto ai metodi di produzione tradizionali. Consentono tempi di produzione più rapidi, una maggiore flessibilità di progettazione e la produzione di componenti più durevoli ed efficienti. Inoltre, consentono la produzione on-demand, che riduce i costi di inventario e semplifica le catene di approvvigionamento.

Un approccio basato sull'economia circolare
Una delle applicazioni più promettenti ed economicamente sostenibili della manifattura additiva in campo energetico è la riparazione di componenti strutturali: la possibilità di riutilizzare un componente usurato, e quindi evitare di produrne uno nuovo, può far risparmiare una notevole quantità di risorse, ridurre i costi e creare nuove opportunità di business. Il tutto promuovendo la sostenibilità e un modello di produzione rispettoso dell'ambiente, perché riciclare gli asset esistenti piuttosto che produrre rifiuti si lega ai principi cardine del paradigma dell'Economia Circolare. I vantaggi nella riparazione di componenti strutturali sono particolarmente grandi quando le parti da riparare sono di grandi dimensioni e ad alto valore aggiunto.
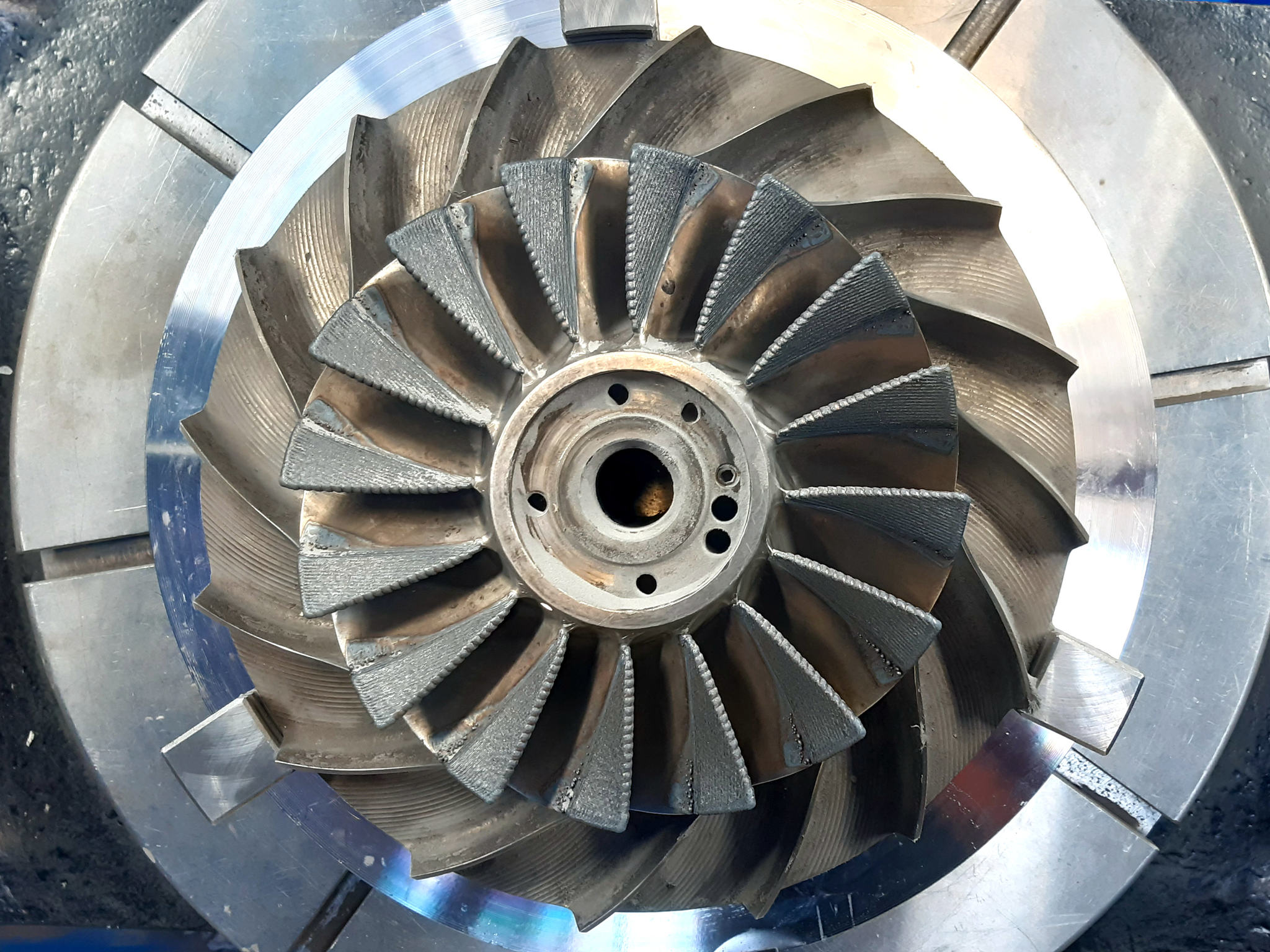
È il caso di uno dei nostri clienti, il leader italiano dell'energia Enel, che si è dotato di una LASERDYNE® 795 di Prima Additive presso la sua centrale elettrica di Santa Barbara (Arezzo, Italia). Grazie a questa soluzione, il cliente è stato in grado di sfruttare importanti vantaggi utilizzando la tecnologia Direct Energy Deposition (DED). Prima Additive ed Enel hanno studiato congiuntamente l'applicazione di riparazione, selezionando una girante centrifuga utilizzata nel sito di produzione geotermica. Normalmente, questo componente si usura dopo un anno di funzionamento continuo e richiederebbe la produzione di un pezzo nuovo ogni anno. Tuttavia, con il sistema LASERDYNE 795 DED e il supporto di Prima Additive, Enel ha qualificato con successo l'applicazione di riparazione dei componenti, rimettendo in funzione le giranti riparate.
La strategia di riparazione è iniziata rettificando il componente danneggiato per creare una superficie piana e omogenea, su cui è stato aggiunto materiale utilizzando la tecnologia DED per ricostruire la forma originale del componente. Gli ingegneri applicativi di Prima Additive hanno creato una replica dell'estremità della girante utilizzando la tecnologia Powder Bed Fusion per studiare e testare la migliore strategia di deposizione. Sono stati valutati diversi approcci costruttivi e si è deciso di utilizzare 3+2 assi per il posizionamento del componente. Utilizzando una lega di acciaio 17-4PH, nota per la sua elevata resistenza meccanica e resistenza all'usura, ci sono volute 2,5 ore per riparare la girante. Enel ha quindi analizzato e certificato il risultato, ha fresato il componente per ripristinarne la geometria originale e prevede di continuare a riparare e riutilizzare queste parti, contribuendo così a un'economia più circolare.
Prima Additive ed Enel continuano a esplorare nuove applicazioni della tecnologia AM, con l'obiettivo di riparare sempre più componenti, ridurre i consumi, i costi e l'impatto ambientale, aprendo così la strada a nuovi modelli di business sostenibili.
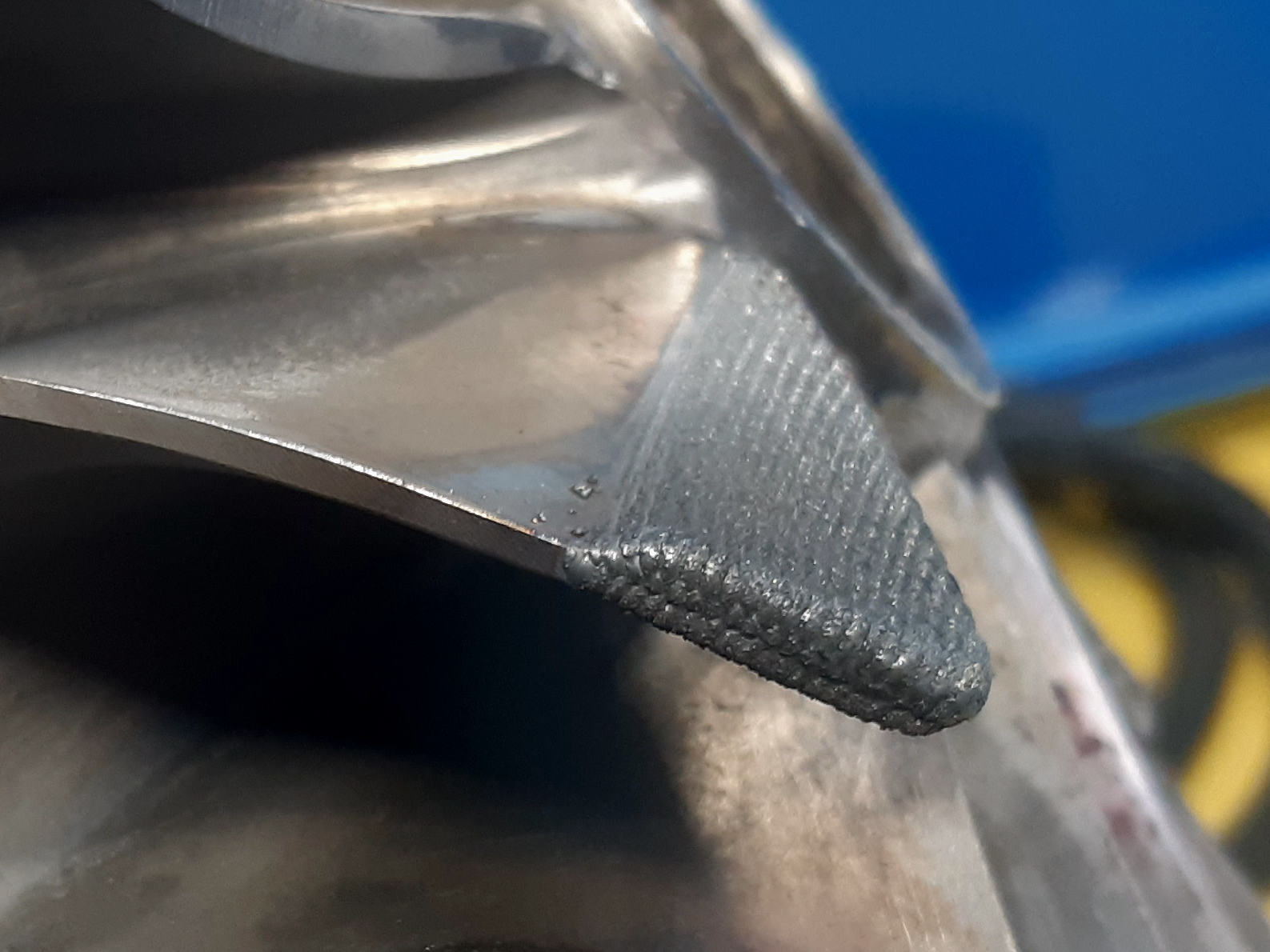
Prima Additive invita le aziende del settore della produzione di energia a esplorare come queste innovative tecnologie di produzione additiva possano migliorare le loro operazioni. Che si tratti di aumentare l'efficienza, ridurre i costi di produzione o promuovere l'innovazione, il nostro team è pronto a fornire consulenza esperta e soluzioni su misura. Contatta Prima Additive oggi stesso per scoprire come la nostra esperienza nell’additive manufacturing può avvantaggiare la tua azienda e aiutarti a raggiungere nuovi traguardi nel competitivo settore energetico.
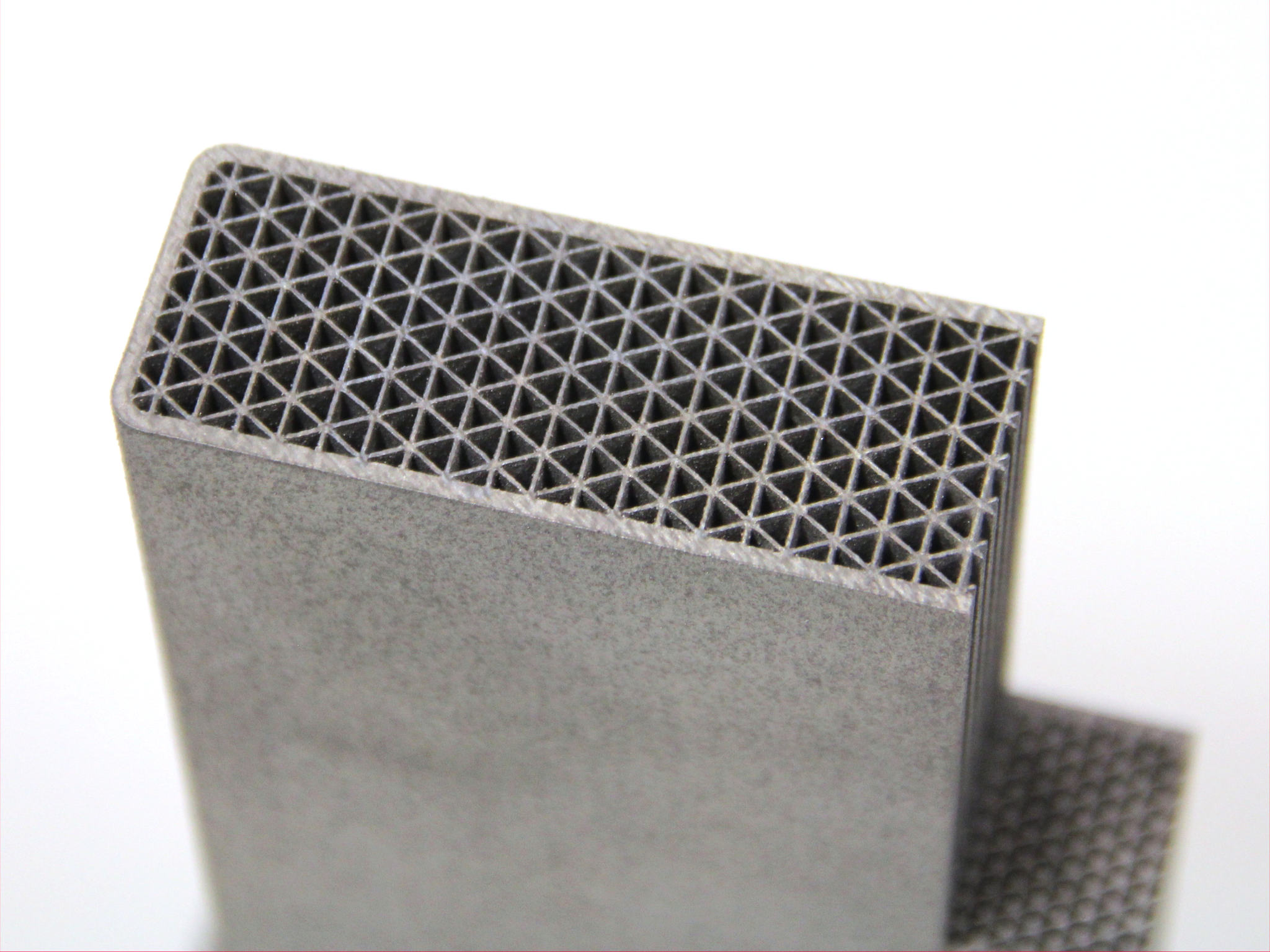